Active adaptive hydraulic ripple cancellation algorithm and system
- Summary
- Abstract
- Description
- Claims
- Application Information
AI Technical Summary
Benefits of technology
Problems solved by technology
Method used
Image
Examples
Embodiment Construction
[0031]Some aspects relate to a system and feed-forward control method of electronically attenuating pressure ripple in a positive displacement pump / motor. Other aspects relate to a method of adapting a model based feed-forward control on the basis of output sensor information.
[0032]Regarding FIG. 8-1, a representative plot of steady state pressure ripple in the time domain is shown for a hydraulic pump / motor operating at constant frequency under a constant torque application. A generated pressure differential signal 8-102 fluctuates in time about a mean pressure differential 8-104 which is substantially constant throughout time. The peak-to-peak amplitude 8-106 of this fluctuating pressure differential signal 8-102 is substantially consistent throughout time as the geometric pattern of the hydraulic pump / motor is symmetric. The peak-to-peak amplitude 8-106 is determined by many characteristics of the hydraulic pump.
[0033]In FIG. 8-2A a representative plot of steady state pressure ri...
PUM
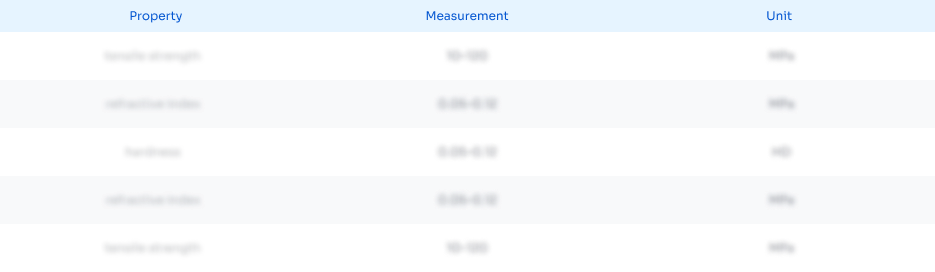
Abstract
Description
Claims
Application Information

- Generate Ideas
- Intellectual Property
- Life Sciences
- Materials
- Tech Scout
- Unparalleled Data Quality
- Higher Quality Content
- 60% Fewer Hallucinations
Browse by: Latest US Patents, China's latest patents, Technical Efficacy Thesaurus, Application Domain, Technology Topic, Popular Technical Reports.
© 2025 PatSnap. All rights reserved.Legal|Privacy policy|Modern Slavery Act Transparency Statement|Sitemap|About US| Contact US: help@patsnap.com