System for developing high pressure shale or tight rock formations using a profusion of open hole sinusoidal laterals
a technology of open hole sinusoidal laterals and high pressure shale, which is applied in the direction of borehole/well accessories, drinking water installation, construction, etc., can solve the problems of high capital cost, high cost of capital, and high cost of water and proppant, and achieves the effect of reducing the ‘relative permeability’, maximizing the capacity of the rock, and reducing the capital cos
- Summary
- Abstract
- Description
- Claims
- Application Information
AI Technical Summary
Benefits of technology
Problems solved by technology
Method used
Image
Examples
Embodiment Construction
[0022]Referring to FIGS. 1, 2 and 3, there is shown a development system comprising a cased wellbore 1 connecting the surface facilities 8 to the lowest casing shoe 2. After the casing shoe the well continues on a path within the shale or tight rock zone 3 as an open hole wellbore 4. This main wellbore 4 usually extends the full length of the targeted shale or tight rock zone. The laterals 6 exit the main wellbore at an open hole kickoff point 5 where the path moves away from the main wellbore. This lateral is drilled in a direction to establish an effective contact surface area in a targeted volume within the shale or tight rock zone.
[0023]As shown in FIG. 2, each lateral targets a volume 7 that will be penetrated in such a direction, both areal and vertical, to optimize the contact surface area within that volume. In essence, the laterals are acting like the individual stages of a multi stage hydraulically fractured well, but instead of creating the contact surface area by many pr...
PUM
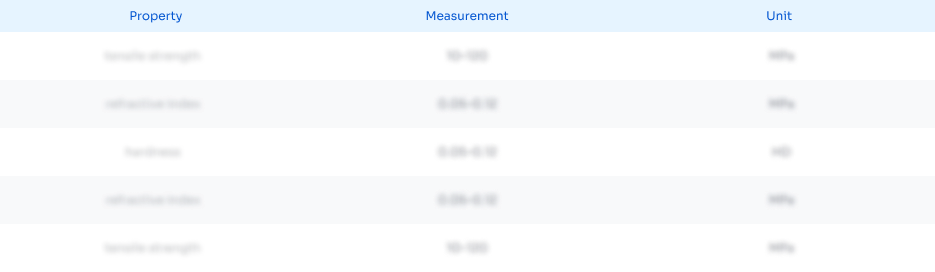
Abstract
Description
Claims
Application Information

- R&D
- Intellectual Property
- Life Sciences
- Materials
- Tech Scout
- Unparalleled Data Quality
- Higher Quality Content
- 60% Fewer Hallucinations
Browse by: Latest US Patents, China's latest patents, Technical Efficacy Thesaurus, Application Domain, Technology Topic, Popular Technical Reports.
© 2025 PatSnap. All rights reserved.Legal|Privacy policy|Modern Slavery Act Transparency Statement|Sitemap|About US| Contact US: help@patsnap.com