Electroactive elastomer actuator and method for the production thereof
- Summary
- Abstract
- Description
- Claims
- Application Information
AI Technical Summary
Benefits of technology
Problems solved by technology
Method used
Image
Examples
Embodiment Construction
[0026]A double film which is band-shaped is shown in FIG. 1 for the construction and production of an electroactive elastomer actuator according to the invention. The double film has a first surface-elastic surface electrode 1, a first electroactive elastomer coating 2, a second surface-elastic surface electrode 3, and a further second electroactive elastomer coating 4. The band-shaped coating material 5, which is configured as a double film, can be produced in the course of an extrusion process or by gluing together two elastomer coatings, which are each provided on one side with a surface electrode. In the illustrated exemplary embodiment, the first and second elastomer coatings 2 and 4 each laterally enclose the surface electrodes 1 and 3, whereby electrical short circuits, for example, due to temporarily occurring moisture bridges, can be prevented.
[0027]The coating material 5, which is to be stockpiled, is wound around a plate-shaped coil form 6 to produce an electroactive elas...
PUM
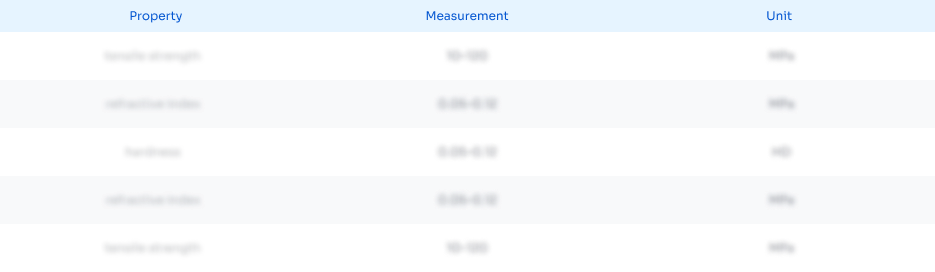
Abstract
Description
Claims
Application Information

- R&D
- Intellectual Property
- Life Sciences
- Materials
- Tech Scout
- Unparalleled Data Quality
- Higher Quality Content
- 60% Fewer Hallucinations
Browse by: Latest US Patents, China's latest patents, Technical Efficacy Thesaurus, Application Domain, Technology Topic, Popular Technical Reports.
© 2025 PatSnap. All rights reserved.Legal|Privacy policy|Modern Slavery Act Transparency Statement|Sitemap|About US| Contact US: help@patsnap.com