Slip Ring Contact Coaxial Connector
- Summary
- Abstract
- Description
- Claims
- Application Information
AI Technical Summary
Benefits of technology
Problems solved by technology
Method used
Image
Examples
Embodiment Construction
[0035]One skilled in the art will appreciate that the connector end 1 and the cable end 3 are descriptors used herein to clarify longitudinal locations and / or contacting interrelationships between the various elements of the coaxial connector(s). In addition to the identified positions in relation to adjacent elements along the coaxial connector longitudinal axis, each individual element has a connector end side and a cable end side, i.e. the sides of the respective element that are facing the respective connector end 1 and the cable end 3 of the coaxial connector 5. A first embodiment of a coaxial connector, as shown in FIGS. 1-6, includes a connector body 7 provided with a connector body bore 9. As best shown in FIG. 2, an annular coupling groove 11 provided in the connector body bore 3 is open to a cable end 3 of the connector body 7. A clamp sidewall 13 of the coupling grove 11 is angled inward from a bottom 15 of the coupling groove 11, dimensioned as a seat against which a lea...
PUM
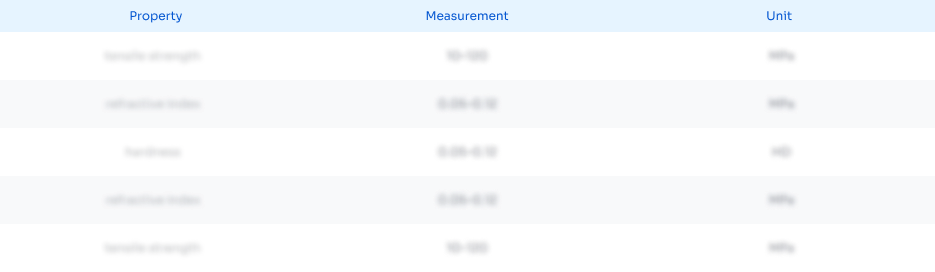
Abstract
Description
Claims
Application Information

- R&D
- Intellectual Property
- Life Sciences
- Materials
- Tech Scout
- Unparalleled Data Quality
- Higher Quality Content
- 60% Fewer Hallucinations
Browse by: Latest US Patents, China's latest patents, Technical Efficacy Thesaurus, Application Domain, Technology Topic, Popular Technical Reports.
© 2025 PatSnap. All rights reserved.Legal|Privacy policy|Modern Slavery Act Transparency Statement|Sitemap|About US| Contact US: help@patsnap.com