Fabrication of high efficiency, high quality, large area diffractive waveplates and arrays
a technology of diffractive waveplates and arrays, which is applied in the field of fabrication of one or two dimensional diffractive waveplate can solve the problems of inability to achieve high-quality dws and their arrays in large area, inability to use grating modulated polarization of output light at macroscopic scales, and inability to produce microscale-period gratings with diffractive properties at optical wavelengths. , to
- Summary
- Abstract
- Description
- Claims
- Application Information
AI Technical Summary
Benefits of technology
Problems solved by technology
Method used
Image
Examples
Embodiment Construction
[0064]Before explaining the disclosed embodiment of the present invention in detail it is to be understood that the invention is not limited in its application to the details of the particular arrangement shown since the invention is capable of other embodiments. Also, the terminology used herein is for the purpose of description and not limitation.
[0065]The preferred embodiment of the present invention shown in FIG. 1A includes a light beam 101 incident upon an optical component 102 capable of converting the incident light beam 101 into a beam with spatially modulated polarization pattern 103. Of particular interest are “cycloidal” and axial modulation patterns shown schematically in FIG. 1B and FIG. 1C, correspondingly, wherein the numerals 106 indicate the linear polarization direction at each point of the plane at the output of the polarization converter (S. R. Nersisyan; et al., “Characterization of optically imprinted polarization gratings,” Appl. Optics 48, 4062, 2009). One p...
PUM
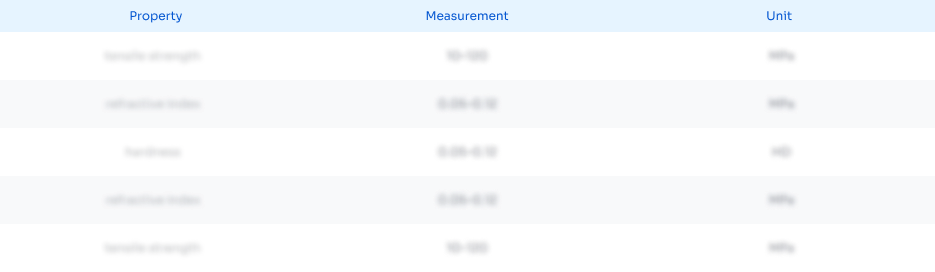
Abstract
Description
Claims
Application Information

- R&D
- Intellectual Property
- Life Sciences
- Materials
- Tech Scout
- Unparalleled Data Quality
- Higher Quality Content
- 60% Fewer Hallucinations
Browse by: Latest US Patents, China's latest patents, Technical Efficacy Thesaurus, Application Domain, Technology Topic, Popular Technical Reports.
© 2025 PatSnap. All rights reserved.Legal|Privacy policy|Modern Slavery Act Transparency Statement|Sitemap|About US| Contact US: help@patsnap.com