Double-layer headbox for a machine for producing a double-layer fibrous web
a technology of fibrous web and headbox, which is applied in the direction of machine wet end, textiles and papermaking, papermaking, etc., can solve the problems of increasing raw material and energy costs, increasing the demands on stream stability,
- Summary
- Abstract
- Description
- Claims
- Application Information
AI Technical Summary
Benefits of technology
Problems solved by technology
Method used
Image
Examples
Embodiment Construction
[0033]FIG. 1 illustrates a schematic longitudinal sectional view of one design form of a headbox nozzle 2 of double-layer headbox 1. The illustrated double-layer headbox 1 is part of a machine which is not depicted in closer detail, for the production of a double-layer fibrous web 3, in particular a double-layer paper or cardboard web consisting of two fibrous suspensions 4.1, 4.2.
[0034]Fibrous suspensions 4.1, 4.2 will generally be suspensions with different fiber stocks; they could however be also suspensions of the same fiber sock, whereby however different physical properties exist.
[0035]Headbox nozzle 2 comprises two converging nozzle chambers 7.1, 7.2 extending across the width B (arrow) and separated from each other on the inside by a separating wedge 5, guiding one respective fibrous suspension 4.1, 4.2 in the form of a fibrous suspension stream 6.1 (arrow), 6.2 (arrow) during operation of double-layer headbox 1. The two nozzle chambers 7.1, 7.2 have the same cross sectional...
PUM
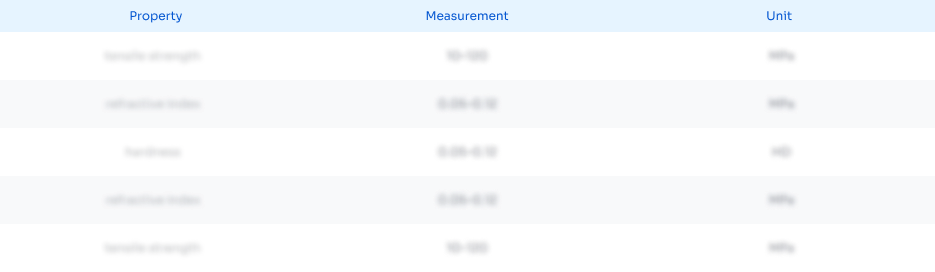
Abstract
Description
Claims
Application Information

- R&D
- Intellectual Property
- Life Sciences
- Materials
- Tech Scout
- Unparalleled Data Quality
- Higher Quality Content
- 60% Fewer Hallucinations
Browse by: Latest US Patents, China's latest patents, Technical Efficacy Thesaurus, Application Domain, Technology Topic, Popular Technical Reports.
© 2025 PatSnap. All rights reserved.Legal|Privacy policy|Modern Slavery Act Transparency Statement|Sitemap|About US| Contact US: help@patsnap.com