Regenerative switched reluctance motor driving system
a technology of switched reluctance motors and driving systems, applied in the direction of motor/generator/converter stoppers, electronic commutators, dynamo-electric converter control, etc., can solve the problems of complex structure, lack of practical use, and reducing the efficiency of three-phase induction motors, so as to improve the energy recovery efficiency, reduce the size and weight, and increase the efficiency of the switched reluctance motor
- Summary
- Abstract
- Description
- Claims
- Application Information
AI Technical Summary
Benefits of technology
Problems solved by technology
Method used
Image
Examples
example 1
[0056]FIG. 1 shows a structure of an electric car to which a regenerative switched reluctance motor driving system according to an embodiment of the present invention is applied. Referring to FIG. 1, the electric car has a DC constant current power supply unit 1, a constant current flip-flop circuit 2, a constant current flip-flop type reluctance motor 3 as a regenerative switched reluctance motor, a differential gear 4 and a mechanical brake 5. Among them, the regenerative switched reluctance motor driving system according to the embodiment of the present invention mainly comprises the DC constant current power supply unit 1, the constant current flip-flop circuit 2 and the constant current flip-flop type reluctance motor 3. Note that although only one multi-phase constant current motor 1 is provided in FIG. 1, it can also be structured to place one for each tire to omit the differential gear 4. In the regenerative switched reluctance motor driving system according to the embodimen...
PUM
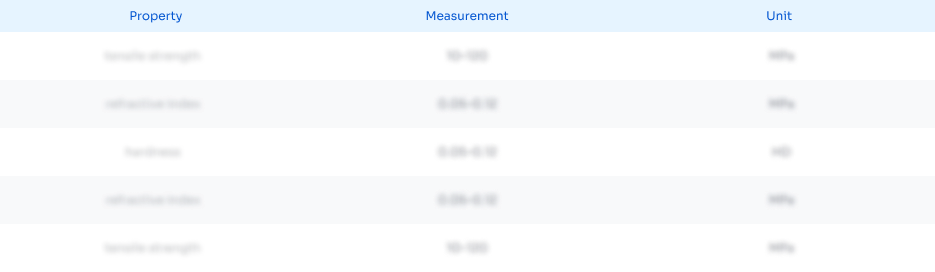
Abstract
Description
Claims
Application Information

- R&D
- Intellectual Property
- Life Sciences
- Materials
- Tech Scout
- Unparalleled Data Quality
- Higher Quality Content
- 60% Fewer Hallucinations
Browse by: Latest US Patents, China's latest patents, Technical Efficacy Thesaurus, Application Domain, Technology Topic, Popular Technical Reports.
© 2025 PatSnap. All rights reserved.Legal|Privacy policy|Modern Slavery Act Transparency Statement|Sitemap|About US| Contact US: help@patsnap.com