Paper sheet multi-feed preventing member
a multi-feed and preventing member technology, applied in the direction of article separation, thin material processing, transportation and packaging, etc., can solve the problems of insufficient separation function, limited paper sheets which the separation pad can separate, and various kinds of paper sheets cannot be reliably separated, etc., to achieve excellent separation function, not easily worn away, and hardly causes vibration and screeching. , the effect of excellent separation function
- Summary
- Abstract
- Description
- Claims
- Application Information
AI Technical Summary
Benefits of technology
Problems solved by technology
Method used
Image
Examples
example 1
Conventional Example 1
[0103]By molding the same kneaded material containing the ingredients shown in Table 1 as the outer layer of Example 1 into a sheet shape with a thickness of 2.0 millimeters, a non-porous paper sheet multi-feed preventing member having a single-layer structure was formed.
[0104]The type A durometer hardness of a measuring sample prepared by using the kneaded material forming the paper sheet multi-feed preventing member was A89 / S as described in Example 1. The friction coefficient was 0.5.
example 2
Conventional Example 2
[0105]By molding the same kneaded material containing the ingredients shown in Table 5 as the outer layer of Example 3 into a sheet shape with a thickness of 2.0 millimeters and vulcanizing it, a non-porous paper sheet multi-feed preventing member having a single-layer structure was formed.
[0106]The type A durometer hardness of a measuring sample prepared by using the kneaded material forming the paper sheet multi-feed preventing member was A90 / S as described in Example 3. The friction coefficient was 0.7.
example 3
Conventional Example 3
[0107]A non-porous paper sheet multi-feed preventing member having a thickness of 2.0 millimeters and a single-layer structure was formed in the same manner as in Conventional example 2 except that the amount of paraffin oil was set to 10 parts by mass as shown in Table 5.
[0108]The type A durometer hardness of a measuring sample prepared by using the kneaded material forming the paper sheet multi-feed preventing member was measured in the same manner as in Example 1, and the result was A75 / S. The friction coefficient was 1.0.
TABLE 5Parts by massConventionalConventionalIngredientexample 2example 3EPDM7070Paraffin oil3010Polypropylene3030Styrenic thermoplastic elastomer2020Crosslinking agent8.48.4Carbon black11
PUM
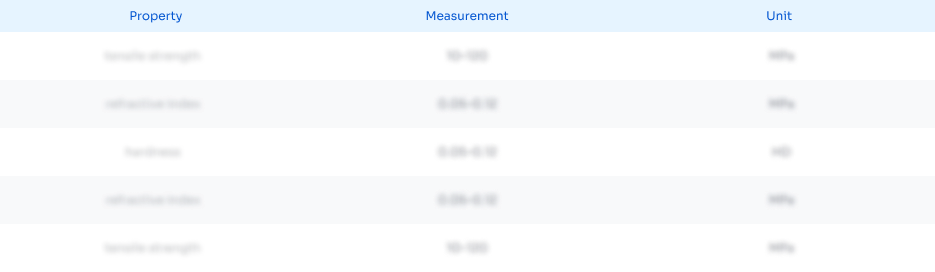
Abstract
Description
Claims
Application Information

- R&D
- Intellectual Property
- Life Sciences
- Materials
- Tech Scout
- Unparalleled Data Quality
- Higher Quality Content
- 60% Fewer Hallucinations
Browse by: Latest US Patents, China's latest patents, Technical Efficacy Thesaurus, Application Domain, Technology Topic, Popular Technical Reports.
© 2025 PatSnap. All rights reserved.Legal|Privacy policy|Modern Slavery Act Transparency Statement|Sitemap|About US| Contact US: help@patsnap.com