Gas check with system for improved loading and retention in bore of muzzleloading firearms
a technology for gas check and muzzleloading firearms, which is applied in the field of gas check with system for muzzleloading firearms, can solve the problems of significant reduction in the efficiency of such firearms, destructive interactions between bullets and bores, and malformed when being placed, so as to reduce the total surface area in contact, facilitate the loading of muzzleloading projectiles, and minimize resistance.
- Summary
- Abstract
- Description
- Claims
- Application Information
AI Technical Summary
Benefits of technology
Problems solved by technology
Method used
Image
Examples
Embodiment Construction
[0031]Referring to the Figures, there are depicted several, but not the only, embodiments of the present invention. In this description, “front” means more towards the open end of the firearm barrel, and the front end of the bullet and gas check are toward the open end of the barrel when the bullet and gas check combination is in the breech (or closed end) of the barrel. “Back” means more towards the butt of the firearm, and the back end of the bullet and the gas check are toward the butt of the firearm when the bullet and gas check combination is in the breach.
[0032]In FIG. 1A is depicted a side, perspective view of a prior art gas check attached to the back of a muzzleloading bullet. Such prior art gas checks may be of the type described by Kearns in U.S. Pat. No. 5,458,064, for example.
[0033]In FIG. 1B is depicted a cross-sectional side view of the prior art gas check 10 of FIG. 1A affixed to a muzzleloading bullet 12 within firearm barrel 14. Bullet 12 has a central hole / recess ...
PUM
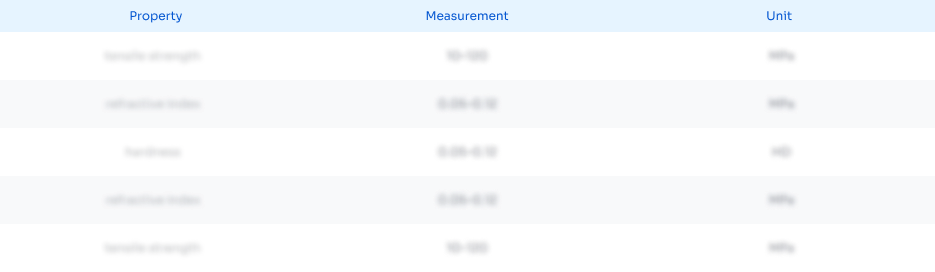
Abstract
Description
Claims
Application Information

- R&D
- Intellectual Property
- Life Sciences
- Materials
- Tech Scout
- Unparalleled Data Quality
- Higher Quality Content
- 60% Fewer Hallucinations
Browse by: Latest US Patents, China's latest patents, Technical Efficacy Thesaurus, Application Domain, Technology Topic, Popular Technical Reports.
© 2025 PatSnap. All rights reserved.Legal|Privacy policy|Modern Slavery Act Transparency Statement|Sitemap|About US| Contact US: help@patsnap.com