Sealed type rotary compressor
a compressor and sealing technology, applied in the direction of positive displacement liquid engines, liquid fuel engines, lighting and heating apparatus, etc., can solve the problems of short supply of oil to the sliding portions, performance deterioration, etc., to achieve the effect of improving oil separation performance, reducing the amount of oil discharged to the outside of the compressor, and efficient oil separation
- Summary
- Abstract
- Description
- Claims
- Application Information
AI Technical Summary
Benefits of technology
Problems solved by technology
Method used
Image
Examples
Embodiment Construction
[0022]Hereinafter, an embodiment of a sealed type rotary compressor of the present invention will be described in detail with reference to the drawings. FIG. 1 is a diagram schematically showing the vertically sectional side surface of an internal high pressure type rotary compressor 1 including first and second rotary compression elements as one embodiment of the sealed type rotary compressor to which the present invention is applied.
[0023]The rotary compressor 1 of the present embodiment is a two-cylinder sealed type rotary compressor in which a rotary compression mechanism 3 including first and second rotary compression elements 10, 20 is received in the lower part of the internal space of a vertically cylindrical sealed container 2 formed of a steel plate and in which an electromotive element 4 is received above the rotary compression mechanism.
[0024]The sealed container 2 is constituted of a container main body 2A in which the electromotive element 4 and the first and second ro...
PUM
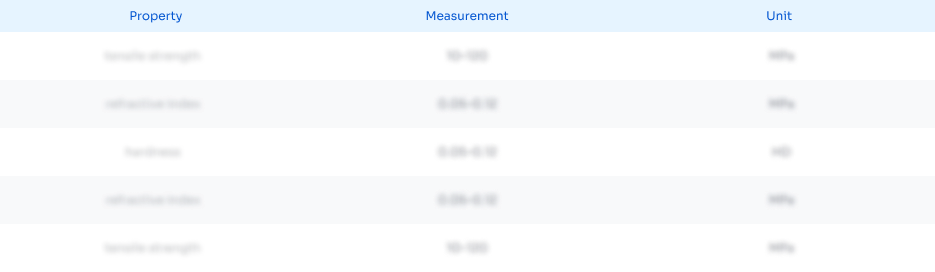
Abstract
Description
Claims
Application Information

- R&D
- Intellectual Property
- Life Sciences
- Materials
- Tech Scout
- Unparalleled Data Quality
- Higher Quality Content
- 60% Fewer Hallucinations
Browse by: Latest US Patents, China's latest patents, Technical Efficacy Thesaurus, Application Domain, Technology Topic, Popular Technical Reports.
© 2025 PatSnap. All rights reserved.Legal|Privacy policy|Modern Slavery Act Transparency Statement|Sitemap|About US| Contact US: help@patsnap.com