Thermal energy storage device
a technology of energy storage device and thermal energy, which is applied in the direction of solar heat storage, machines/engines, light and heating equipment, etc., can solve the problems of low efficiency, high cost, and inability to achieve significant commercialization
- Summary
- Abstract
- Description
- Claims
- Application Information
AI Technical Summary
Problems solved by technology
Method used
Image
Examples
Embodiment Construction
Overview
[0040]The present application provides a thermal energy storage (“TES”) and transfer device for storing thermal energy generated by a thermal energy source and transferring it to a different physical location. The stored thermal energy may be used at a later time by a recipient structure or device such as a thermal energy driven power generation device or any other device requiring thermal energy (e.g., a Stirling engine or a steam turbine). The TES device may be described as a buffering means for thermal energy supplied by a thermal energy source before the thermal energy is provided to the recipient structure or device. Thus, the TES device may be used to introduce a delay period between the generation of the thermal energy and its consumption by a thermal energy driven power generation device. Alternatively, the TES device may be configured to provide thermal energy to a thermal energy driven power generation device without introducing a delay. As will be described below,...
PUM
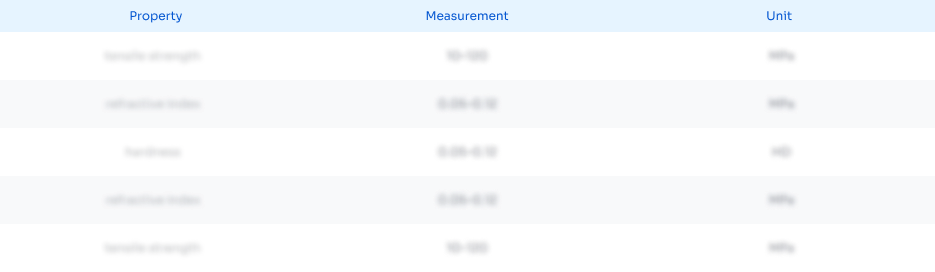
Abstract
Description
Claims
Application Information

- R&D
- Intellectual Property
- Life Sciences
- Materials
- Tech Scout
- Unparalleled Data Quality
- Higher Quality Content
- 60% Fewer Hallucinations
Browse by: Latest US Patents, China's latest patents, Technical Efficacy Thesaurus, Application Domain, Technology Topic, Popular Technical Reports.
© 2025 PatSnap. All rights reserved.Legal|Privacy policy|Modern Slavery Act Transparency Statement|Sitemap|About US| Contact US: help@patsnap.com