Methods and structures for the production of electrically treated items and electrical connections
- Summary
- Abstract
- Description
- Claims
- Application Information
AI Technical Summary
Benefits of technology
Problems solved by technology
Method used
Image
Examples
example 1
[0209]The following solid ingredients were weighed out:
[0210]1. 33 grams of Kraton (Kraton 1450 Kraton Polymers)
[0211]2. 16.5 grams of carbon black (Vulcan XC-72 Cabot Corporation)
[0212]3. 0.5 grams of elemental sulfur
[0213]These solid ingredients were mixed and dissolved in approximately 10 ounces of a xylene solvent. This produced a fluid ink / coating formulation which, after drying, consisted of:
[0214]1. Kraton=66%
[0215]2. Carbon Black=33%
[0216]3. Sulfur=1%
[0217]A length of PET film was coated with this ink / coating solution in the form of a 1 inch wide buss stripe pattern. The stripe pattern was allowed to dry and then was immersed as a cathode in a standard Watts nickel plating bath similar to that depicted in FIG. 17. The PET film was pulled through the bath at a rate of approximately 3 inches per minute. The stripe pattern covered quickly with nickel electrodeposit. At an applied contact potential of 3 volts, the electrodeposit growth front maintained its position approximately...
example 2
[0218]A piece of PET sheet 4 mil thick was cut into a sheet of linear dimensions 13 inch by 8.5 inch. This sheet was then wrapped around a polyethylene pipe having a 4 inch diameter. A DER strip, 1 inch wide was applied as a simulated buss on the exterior of the PET sheet extending circumferentially around the pipe. A length of copper wire, 0.019 inch in diameter was then wrapped around the pipe overlaying and in contact with the DER buss. The pipe / PET / DER buss / copper wire assembly was immersed in a standard Watts nickel electroplating bath and the copper wire was made cathodic at 3 volts overall potential relative to the anode. It was observed that the buss completely covered with nickel electrodeposit in 15 seconds. This shows that very rapid coverage of extended lengths of buss can be achieved with this approach. The approach therefore allows linear web process speeds to be greatly increased.
[0219]One intent of the electroplating processes and embodiments of FIGS. 17-37 is to ach...
PUM
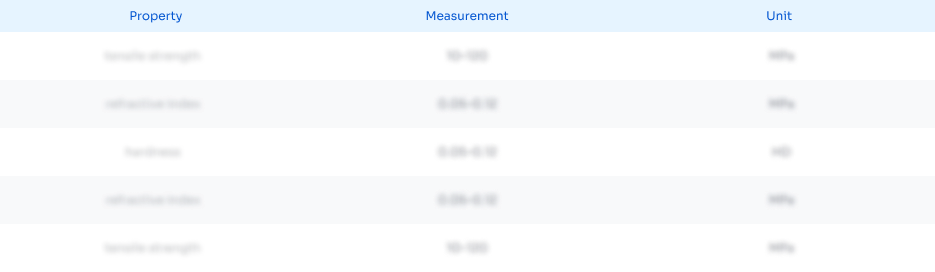
Abstract
Description
Claims
Application Information

- R&D
- Intellectual Property
- Life Sciences
- Materials
- Tech Scout
- Unparalleled Data Quality
- Higher Quality Content
- 60% Fewer Hallucinations
Browse by: Latest US Patents, China's latest patents, Technical Efficacy Thesaurus, Application Domain, Technology Topic, Popular Technical Reports.
© 2025 PatSnap. All rights reserved.Legal|Privacy policy|Modern Slavery Act Transparency Statement|Sitemap|About US| Contact US: help@patsnap.com