Heat Exchanger
- Summary
- Abstract
- Description
- Claims
- Application Information
AI Technical Summary
Benefits of technology
Problems solved by technology
Method used
Image
Examples
Embodiment Construction
[0039]The objective is achieved by using a core assembly manufactured in part or in full as a one-piece monolithic metallic block, similar in configuration to a conventional fin-and-plate heat exchanger. In such a structure, the brazing seams, which usually are a source for imperfections and internal leakages, have been eliminated. All the voids in the suggested construction allowing the passage of both the hot and cold flows are obtained by removal of material from a single piece of metal.
[0040]FIGS. 5, 6 show one embodiment of the invention where a core assembly is manufactured as a one-piece monolithic metallic block 15 having two sets of parallel and mutually perpendicular flow channels 16 and 17. Each of these channels are provided for one of the hot and cold flow passages.
[0041]The aggregate volume of channels 16 (FIGS. 5, 6) and their respective headers 38 and 39 (FIG. 14) form a confined space for the cold flow passage, while the aggregate volume of Channels 17 (FIGS. 5, 6) ...
PUM
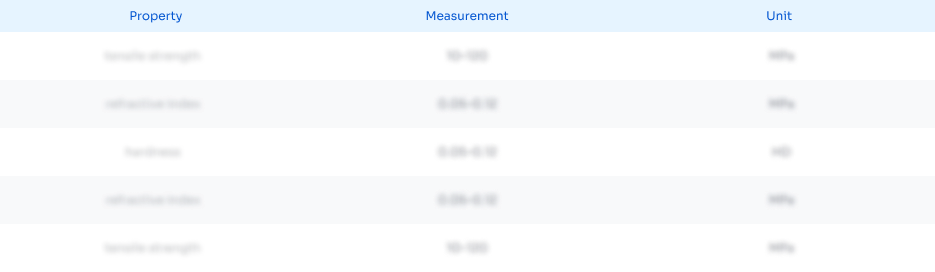
Abstract
Description
Claims
Application Information

- R&D
- Intellectual Property
- Life Sciences
- Materials
- Tech Scout
- Unparalleled Data Quality
- Higher Quality Content
- 60% Fewer Hallucinations
Browse by: Latest US Patents, China's latest patents, Technical Efficacy Thesaurus, Application Domain, Technology Topic, Popular Technical Reports.
© 2025 PatSnap. All rights reserved.Legal|Privacy policy|Modern Slavery Act Transparency Statement|Sitemap|About US| Contact US: help@patsnap.com