Method and apparatus for detecting damage in armor structures
a technology for armor structures and damage detection, applied in the direction of mechanical measurement arrangements, mechanical roughness/irregularity measurements, instruments, etc., can solve the problems of limited field application value, general inconvenient method, and damage to ceramic plates
- Summary
- Abstract
- Description
- Claims
- Application Information
AI Technical Summary
Benefits of technology
Problems solved by technology
Method used
Image
Examples
first embodiment
[0031]FIG. 2A illustrates a damage detection system 20 for armor structures according to the present disclosure. System 20 includes a sensor embedded armor structure 10, a signal interface device 22 which interfaces between armor structure 10 and a computer 24 configured to run a software module that controls the interface device 22, determines actuation drive signal levels transmitted to transducers 1-4, analyzes received signals detected by transducers 1-4 when operated in sensor mode, and determines the location and severity of damage in the armor structure 10.
second embodiment
[0032]FIG. 2B illustrates a damage detection system 30 for armor structures according to the present disclosure. In this embodiment, a hand held interrogation device 32 includes a digital signal processor (DSP) to implement the data analysis and damage detection. This DSP and the actuation and data acquisition circuits may be integrated into the single handheld device 32, such that no external computer is required to actuate transducers embedded in armor structure 10 or analyze the received signals resulting therefrom.
Sensors and Cables
[0033]Any necessary sensors and / or cables may be attached in any conventional manner known in the art. For example, a layer (e.g., a flexible circuit board) containing the sensors (e.g., transducers 1-4) attached thereto may be embedded or bonded to the armor structure 10 such that the transducers are effectively mechanically coupled to the structure 10 to generate and detect elastic wave signals. One may also use individually placed sensors for the s...
PUM
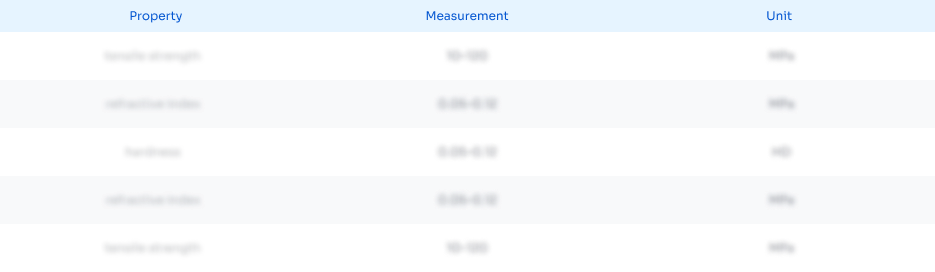
Abstract
Description
Claims
Application Information

- R&D Engineer
- R&D Manager
- IP Professional
- Industry Leading Data Capabilities
- Powerful AI technology
- Patent DNA Extraction
Browse by: Latest US Patents, China's latest patents, Technical Efficacy Thesaurus, Application Domain, Technology Topic, Popular Technical Reports.
© 2024 PatSnap. All rights reserved.Legal|Privacy policy|Modern Slavery Act Transparency Statement|Sitemap|About US| Contact US: help@patsnap.com