Sewing machine
a sewing machine and needle technology, applied in the field of sewing machines, can solve the problems of complicated operation, large time and labor, and achieve the effect of enhancing the operability of the sewing machine, facilitating the work of inserting, and smoothing the transition to sewing operation
- Summary
- Abstract
- Description
- Claims
- Application Information
AI Technical Summary
Benefits of technology
Problems solved by technology
Method used
Image
Examples
first exemplary embodiment
Advantage of First Exemplary Embodiment
[0109]As described above, according to the sewing machine 1 of the first exemplary embodiment, when the thread discharging hole 112 of the thread pipe 110 is moved to the threading position by means of the coupling member 161, the air ejecting unit 130 is moved to the ejecting position. Similarly, when the air ejecting unit 130 is moved to the ejecting position, the thread discharging hole 112 of the thread pipe 110 is moved to the threading position. Namely, when the operation lever 4 is operated to operate one of the thread guide lever 121 or the air ejection moving means, the other can also be operated at the same time. Thus, an operation for inserting the lower looper thread T through the lower looper 21 is simplified as compared with the background art. In addition, an certain operating procedure is not required. Therefore, the threading operation can easily be carried out. Thus, it is possible to enhance operability of the sewing machine ...
second exemplary embodiment
Advantage of Second Exemplary Embodiment
[0133]According to the sewing machine 1 of the second exemplary embodiment, the thread guide lever 121 supporting the thread pipe 110 and the air ejecting unit 230 can be electrically controlled by driving the stepping motor 270. In addition, they can be controlled at the same time via the coupling member 261. In other words, the coupling member 261 and the actuator (the stepping motor 270) which drives the coupling member 261 enables a simultaneous control of the thread guide lever 121 and the air ejecting unit 230 without increasing much cost. Accordingly, the threading operation can be carried out more easily than in the background art. Thus, the operability of the sewing machine 1 can be enhanced.
Others
[0134]As shown in FIG. 10, a guide member 167 (returning means) may be may be fixed and provided in a bed portion of the sewing machine frame M. The guide member 167 positions the thread discharging hole 112 of the thread pipe 110 to the ret...
PUM
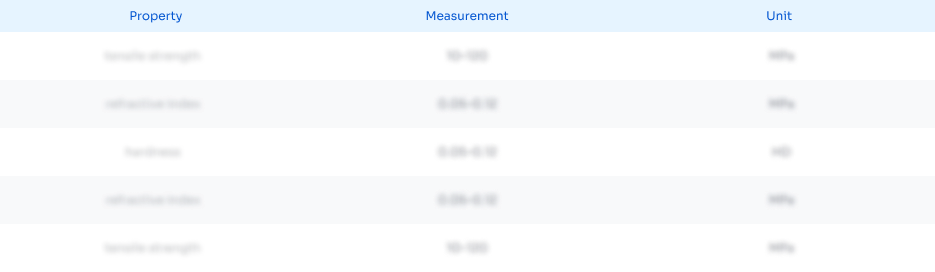
Abstract
Description
Claims
Application Information

- R&D
- Intellectual Property
- Life Sciences
- Materials
- Tech Scout
- Unparalleled Data Quality
- Higher Quality Content
- 60% Fewer Hallucinations
Browse by: Latest US Patents, China's latest patents, Technical Efficacy Thesaurus, Application Domain, Technology Topic, Popular Technical Reports.
© 2025 PatSnap. All rights reserved.Legal|Privacy policy|Modern Slavery Act Transparency Statement|Sitemap|About US| Contact US: help@patsnap.com