Low-mass-trigger controlled release of projectiles having variable energies and numbers in a centrifugal propulsion weapon, and methods of weapon use
a centrifugal propulsion and variable energy technology, applied in the direction of weapons, launching weapons, white arms/cold weapons, etc., can solve the problems of limited projectile speed, inability to feed the desired amount of projectiles in any centrifugal operated weapon, and the power required to rotate the radial barrel is too great to develop an economically feasible rapid fire weapon, etc., to achieve the effect of high ra
- Summary
- Abstract
- Description
- Claims
- Application Information
AI Technical Summary
Benefits of technology
Problems solved by technology
Method used
Image
Examples
first embodiment
[0083]FIG. 1 is top plan view of a centrifugal having a first embodiment projectile release mechanism in accordance with the related predecessor invention in use for ejecting projectiles, by way of illustration in burst of six projectiles each burst.
[0084]FIG. 2 is a detail top plan view at expanded scale of the first embodiment projectile release mechanism in accordance with the related predecessor invention at a first time and in a first, projectile-ejection-obstructing, position.
[0085]FIG. 3 is a detail top plan view at expanded scale of the first embodiment projectile release mechanism in accordance with the related predecessor invention at a second time and in a second, projectile-ejection-enabling, position.
[0086]FIG. 4 is a detail top plan view at expanded scale of the first embodiment projectile release mechanism in accordance with the related predecessor invention at a third time and in a third, projectile-ejection-obstructing, position with a previously gated projectile st...
second embodiment
[0092]FIG. 10 is a side view of a centrifugal gun having an improved, second embodiment, projectile release trigger mechanism in accordance with the present invention.
[0093]FIG. 11 is a view of an exemplary three arm selectors which, in their movement relative to a case, are a substantial part of the realization of the improved second embodiment of the projectile release mechanism in accordance with the present invention previously seen in part in FIG. 11.
[0094]FIGS. 12 and 13 show the detail movement of an arm within the previous, first embodiment, projectile release trigger mechanism for a centrifugal gun, previously seen in FIGS. 1-7, in accordance with the related predecessor inventions.
[0095]FIGS. 14 and 15 show movement of a selector, replacing the arm of FIGS. 12 and 13, within the improved, second embodiment, projectile release trigger mechanism for a centrifugal gun in accordance with the present invention
[0096]FIG. 16 shows a handle bar assembly within the improved, second...
third embodiment
[0099]FIG. 19, consisting of FIGS. 19a and 19b, are respective top and side plan views of a centrifugal gun having an improved, third embodiment, projectile release trigger mechanism in accordance with the present invention in a first, projectile-release-obstructing, position.
[0100]FIG. 20, consisting of FIGS. 20a and 20b, are respective top and side plan views of a centrifugal gun with the improved, third embodiment, projectile release trigger mechanism in accordance with the present invention previously seen in FIG. 19, this third embodiment of the release mechanism now in a second, projectile-releasing, position.
PUM
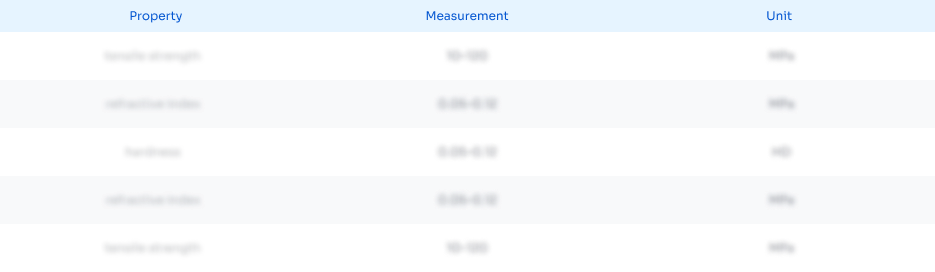
Abstract
Description
Claims
Application Information

- R&D
- Intellectual Property
- Life Sciences
- Materials
- Tech Scout
- Unparalleled Data Quality
- Higher Quality Content
- 60% Fewer Hallucinations
Browse by: Latest US Patents, China's latest patents, Technical Efficacy Thesaurus, Application Domain, Technology Topic, Popular Technical Reports.
© 2025 PatSnap. All rights reserved.Legal|Privacy policy|Modern Slavery Act Transparency Statement|Sitemap|About US| Contact US: help@patsnap.com