Supercharger with heat insulated gear case
a supercharger and gear case technology, applied in the direction of machines/engines, liquid fuel engines, rotary/oscillating piston pump components, etc., can solve the problems of catastrophic supercharger damage, limited problem, and inability to maintain high speed and load at high speed and load, and achieve the effect of low cos
- Summary
- Abstract
- Description
- Claims
- Application Information
AI Technical Summary
Benefits of technology
Problems solved by technology
Method used
Image
Examples
Embodiment Construction
[0017]Referring first to FIG. 1 of the drawings in detail, numeral 10 generally indicates a positive displacement helical lobed compressor or supercharger according to the invention. Supercharger 10 includes a rotor housing 12 having an internal rotor cavity 14 defined by a surrounding wall 16 and front and rear end walls 18, 20 respectively. A generally rectangular inlet opening 22 in a lower portion of the rear end wall 20 communicates an inlet end 23 of the cavity 14 with a source of inlet air, not shown. A generally V-shaped outlet opening 24 extends through the surrounding wall 16 adjacent the front end wall 18 of the housing and communicates an outlet end 25 of the cavity 14 with a pressure charging air system, not shown.
[0018]Within the cavity 14 there are rotatably mounted a pair of supercharger rotors 26, 28 having lobes 30, 32 with opposite helix angles, as is best shown in FIG. 2. The lobes 30, 32 of the rotors are interleaved in assembly to define with the housing helica...
PUM
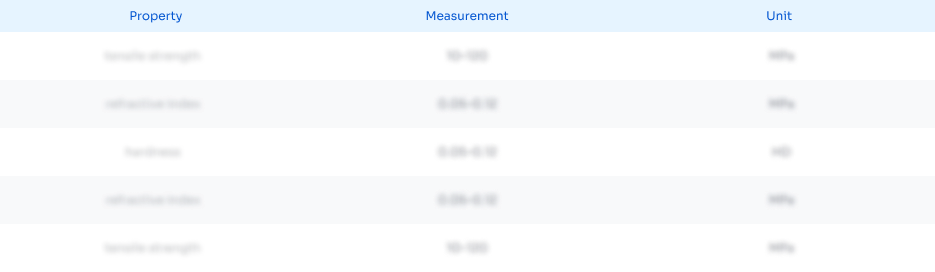
Abstract
Description
Claims
Application Information

- R&D
- Intellectual Property
- Life Sciences
- Materials
- Tech Scout
- Unparalleled Data Quality
- Higher Quality Content
- 60% Fewer Hallucinations
Browse by: Latest US Patents, China's latest patents, Technical Efficacy Thesaurus, Application Domain, Technology Topic, Popular Technical Reports.
© 2025 PatSnap. All rights reserved.Legal|Privacy policy|Modern Slavery Act Transparency Statement|Sitemap|About US| Contact US: help@patsnap.com