Cryogenic Air Separation Process and Apparatus
a technology of cryogenic air and separation process, which is applied in the direction of lighting and heating apparatus, refrigeration and liquid storage, solidification, etc., can solve the problems of increasing the size and power consumption of the cosub>2 /sub>recovery unit, and becoming very costly and difficult to recover and capture the cosub>2 /sub>. , to achieve the effect o
- Summary
- Abstract
- Description
- Claims
- Application Information
AI Technical Summary
Benefits of technology
Problems solved by technology
Method used
Image
Examples
Embodiment Construction
[0056]The invention will be described in greater detail with reference to the figures, wherein FIG. 1 represents the Prior art approach in which the air separation unit simply supplies the oxygen to the power plant. FIGS. 2 and 3 represent an air separation unit operating according to the invention at different periods, FIGS. 4 and 5 represent different phases of operation of plant according to the prior art and FIGS. 6, 7 and 8 represent an air separation units capable of operating according to the invention.
[0057]As shown on FIG. 1 for the Prior art, during peaks in power demand, 1000 Nm3 / h of feed air 6 is treated to yield 200 Nm3 / h of oxygen 12 required for peak demand by power generation plant 10. If the demand is reduced, less air is sent to the oxygen plant 13 to yield less oxygen. The air flow is essentially proportional to the oxygen demand.
[0058]As shown on FIG. 2 for the bascule approach, during peaks in power demand, 110 Nm3 / h of liquid oxygen 53 from a liquid oxygen tan...
PUM
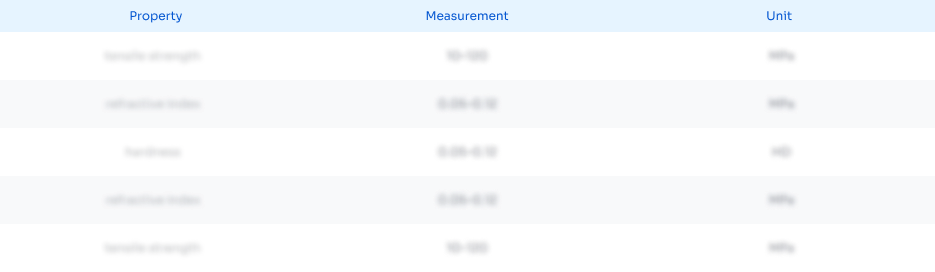
Abstract
Description
Claims
Application Information

- R&D
- Intellectual Property
- Life Sciences
- Materials
- Tech Scout
- Unparalleled Data Quality
- Higher Quality Content
- 60% Fewer Hallucinations
Browse by: Latest US Patents, China's latest patents, Technical Efficacy Thesaurus, Application Domain, Technology Topic, Popular Technical Reports.
© 2025 PatSnap. All rights reserved.Legal|Privacy policy|Modern Slavery Act Transparency Statement|Sitemap|About US| Contact US: help@patsnap.com