Apparatus for endpoint detection during polishing
a technology of endpoint detection and polishing, which is applied in the direction of grinding machine components, manufacturing tools, lapping machines, etc., can solve the problems of wafer over-polishing, increasing the complexity of microstructured components, and requiring higher inspection precision and better accuracy of each manufacturing process, so as to improve detection accuracy
- Summary
- Abstract
- Description
- Claims
- Application Information
AI Technical Summary
Benefits of technology
Problems solved by technology
Method used
Image
Examples
first embodiment
[0033] The configuration of the sensing element 31 are selected basing on actual detection requirement, which can be an optical sensor 311, an eddy current sensor 312, or the combination of the two, as shown in FIG. 4, or other sensing devices. As the first preferred embodiment shown in FIG. 4, the sensing element is the combination of the optic sensor 311 and the eddy current sensor 312 so as to enhance the accuracy and quality of the detection since the workpiece is made of metallic material. That is, any sensor suitable for detection polishing status of a workpiece can be used as the sensing element.
[0034] The linear motion of displacement 91 is realized by a linear moving mechanism, such as a linear rail 32 shown in FIG. 4. The sensing element 31 is being disposed on a linear rail 32 while the linear rail 32 is arranged in the probe 30 such that the sensing element 31 can be driven to proceed a linear motion of displacement 91 along the linear rail 32 while enabling the same to ...
second embodiment
[0035] Please refer to FIG. 5, which is a schematic diagram of a second preferred embodiment according to the present invention. As seen in FIG. 5, there are a plurality of sensing elements 61 being arranged on the probe 60 of the endpoint detection apparatus 6, and the plural sensing elements 61 are being separated from each other by a specific interval while each is capable of being driven to proceed a linear motion of displacement 91 along a linear rail 64 arranged on the probe 60. the invention shown in FIG. 5, which allows a larger detection range, is suitable to be used for detecting a large-sized workpiece since the displacement of each sensing element 61 is small and thus the accuracy of detection inversely affected thereby is reduced.
[0036] Please refer to FIG. 6, which is a schematic diagram showing the assembly of a polishing device and an endpoint detection apparatus of the invention. The polishing device 7, which can be a mechanical polishing device but is not limited t...
PUM
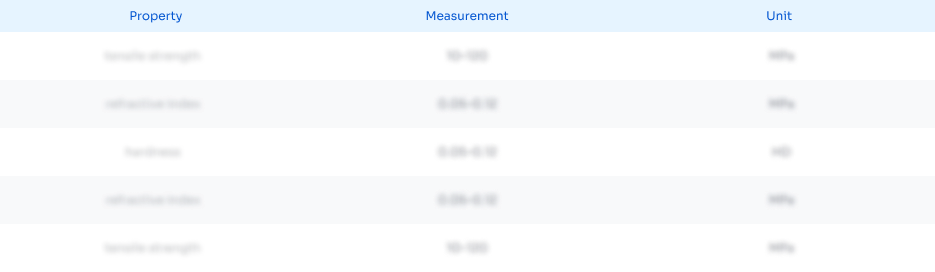
Abstract
Description
Claims
Application Information

- Generate Ideas
- Intellectual Property
- Life Sciences
- Materials
- Tech Scout
- Unparalleled Data Quality
- Higher Quality Content
- 60% Fewer Hallucinations
Browse by: Latest US Patents, China's latest patents, Technical Efficacy Thesaurus, Application Domain, Technology Topic, Popular Technical Reports.
© 2025 PatSnap. All rights reserved.Legal|Privacy policy|Modern Slavery Act Transparency Statement|Sitemap|About US| Contact US: help@patsnap.com