Controlling system for cooling fan
a control system and fan technology, applied in the direction of rotors, marine propulsion, vessel construction, etc., can solve the problems of drastic change in fan noise, drastic change in motor speed within a period, and sudden change in fan speed, so as to reduce the drastic fluctuation of consumption power and stabilize the operating power
- Summary
- Abstract
- Description
- Claims
- Application Information
AI Technical Summary
Benefits of technology
Problems solved by technology
Method used
Image
Examples
first embodiment
[0022] the present invention will be described below with reference to FIGS. 1 to 4.
[0023]FIG. 1 illustrates an example in which a radiator 2 serving as the engine cooling device and an oil cooler 3 serving as the working-oil cooling device are cooled with a single cooling fan 1. Therefore, in this example, fluids to be cooled include working oil and coolant water for the radiator 2.
[0024] In FIG. 1, a hydraulic motor 4 is provided for driving the cooling fan 1, and a variable-displacement hydraulic pump 5 is provided as a hydraulic source for the hydraulic motor 4. Moreover, a controller 6 and a pump regulator 7 define speed controlling means for controlling the rotational speed of the hydraulic motor 4. In some cases, the rotational speed will be referred to as a fan speed hereinafter.
[0025] Specifically, the pump regulator 7 is actuated in response to a command signal from the controller 6, by which the capacity of the hydraulic pump 5 is adjusted. Thus, the pump pressure is co...
second embodiment
[0041] A second embodiment according to the present invention will now be described with reference to FIGS. 5 and 6.
[0042] The description of the second embodiment below will only include the differences from the first embodiment.
[0043] Even when the cooling fan 1 rotates at a constant rotational speed, the cooling effect may vary depending on the outside air temperature. In other words, the higher the outside air temperature, the lower the cooling effect, whereas the lower the outside air temperature, the higher the cooling effect. Furthermore, the outside air temperature may also vary by several tens of degrees Celsius depending on location and season.
[0044] Generally, the fan function is set such that a proper cooling capability is attained even when the outside air temperature is at the highest.
[0045] Consequently, controlling the motor speed simply on the basis of the water temperature and the oil temperature may possibly cause overcooling as a result of an excess cooling ca...
PUM
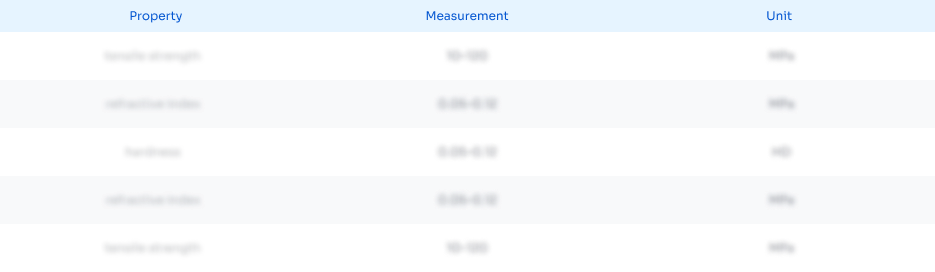
Abstract
Description
Claims
Application Information

- R&D
- Intellectual Property
- Life Sciences
- Materials
- Tech Scout
- Unparalleled Data Quality
- Higher Quality Content
- 60% Fewer Hallucinations
Browse by: Latest US Patents, China's latest patents, Technical Efficacy Thesaurus, Application Domain, Technology Topic, Popular Technical Reports.
© 2025 PatSnap. All rights reserved.Legal|Privacy policy|Modern Slavery Act Transparency Statement|Sitemap|About US| Contact US: help@patsnap.com