Regenerative thermal oxidizer
a regenerative thermal oxidizer and oxidizer technology, applied in the direction of combustion types, heating types, stoves or ranges, etc., can solve the problems of materially affecting the efficiency of regenerative thermal oxidizers, short circuiting of oxidizers, and potential for polluting the environment, and achieve the effect of relatively constant pressure of fluid through the regenerative thermal oxidizer
- Summary
- Abstract
- Description
- Claims
- Application Information
AI Technical Summary
Benefits of technology
Problems solved by technology
Method used
Image
Examples
Embodiment Construction
[0011]FIGS. 1-12 show a schematic representation of one embodiment of a regenerative thermal oxidizer system in accordance with the present invention, although the present invention is applicable to oxidizer systems having other known configurations. As seen in FIGS. 1-12, a two chamber regenerative oxidizer 20 comprises a common combustion chamber 22 overlying a pair of conventional segregated regenerative chambers 24 and 26. The combustion chamber 22 is provided with one or more conventional burners 30a and 30b. In the embodiment shown, a first burner 30a is provided in combustion chamber 22 proximate regenerative chamber 24 and a second burner 30b is provided in combustion chamber 22 proximate regenerative chamber 26. While the embodiment of the oxidizer disclosed herein shows burners 30a and 30b positioned proximate chambers 24 and 26, the burners are not necessarily positioned proximate chambers 24 and 26, and may be positioned at any of a variety of alternative locations withi...
PUM
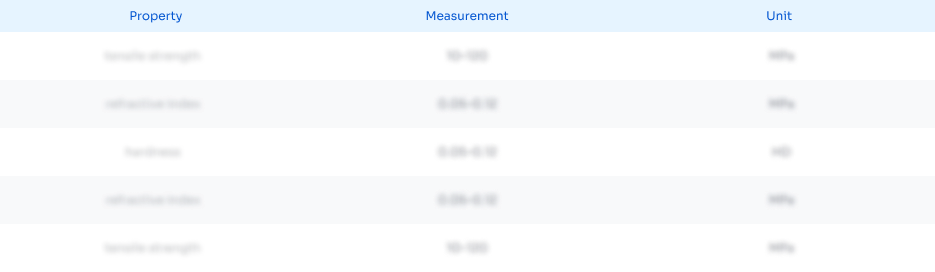
Abstract
Description
Claims
Application Information

- Generate Ideas
- Intellectual Property
- Life Sciences
- Materials
- Tech Scout
- Unparalleled Data Quality
- Higher Quality Content
- 60% Fewer Hallucinations
Browse by: Latest US Patents, China's latest patents, Technical Efficacy Thesaurus, Application Domain, Technology Topic, Popular Technical Reports.
© 2025 PatSnap. All rights reserved.Legal|Privacy policy|Modern Slavery Act Transparency Statement|Sitemap|About US| Contact US: help@patsnap.com