Infinitely adjustable engagement system and method
a technology of engagement system and adjustable height, which is applied in the direction of friction lining, machines/engines, couplings, etc., can solve the problems of limited step size, limited spacing between teeth, and limited step size, etc., to achieve the effect of limiting step size and utility for high-precision applications
- Summary
- Abstract
- Description
- Claims
- Application Information
AI Technical Summary
Benefits of technology
Problems solved by technology
Method used
Image
Examples
Embodiment Construction
[0015] Exemplary embodiments are described with reference to specific configurations. Those of ordinary skill in the art will appreciate that various changes and modifications can be made while remaining within the scope of the appended claims. Additionally, well-known elements, materials, devices, components, methods, process steps and the like may not be set forth in detail in order to avoid obscuring the invention.
[0016] The systems and methods of the present invention may be used in a wide variety of applications where precise and secure engagement of two or more bodies is required. The invention may be used in connection with linear motors (stepper, DC brushed and brushless servo, inductance and AC synchronous, etc.), gearing systems, clamping systems, medical / surgical applications, dental applications, eyeglass applications, optical applications, precision placement applications and various other applications requiring fast-acting, high holding force, infinite step size resol...
PUM
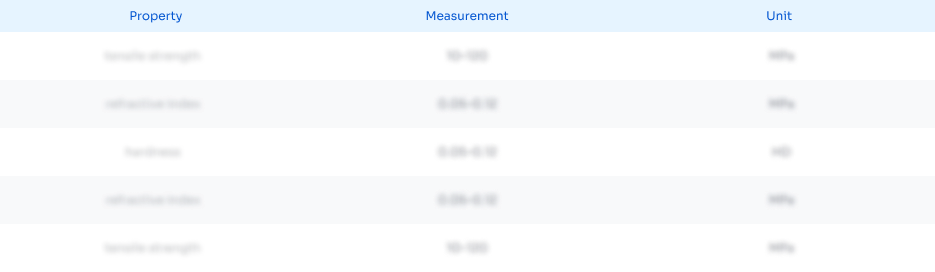
Abstract
Description
Claims
Application Information

- R&D
- Intellectual Property
- Life Sciences
- Materials
- Tech Scout
- Unparalleled Data Quality
- Higher Quality Content
- 60% Fewer Hallucinations
Browse by: Latest US Patents, China's latest patents, Technical Efficacy Thesaurus, Application Domain, Technology Topic, Popular Technical Reports.
© 2025 PatSnap. All rights reserved.Legal|Privacy policy|Modern Slavery Act Transparency Statement|Sitemap|About US| Contact US: help@patsnap.com