Floor sheet assembly
a technology of floor sheet and assembly, which is applied in the direction of building components, constructions, buildings, etc., can solve the problems of increasing the gross weight of the vehicle, the floor of the vehicle, and not being appropriate, and achieve the effect of efficient absorption of noise generated
- Summary
- Abstract
- Description
- Claims
- Application Information
AI Technical Summary
Benefits of technology
Problems solved by technology
Method used
Image
Examples
example
[0035] Description is given of an example (test results) of sound absorption obtained by the floor sheet assembly 1 according to the embodiment described above. Conditions under which testing was carried out are as follows:
(1) material for an intermediate member 10 and sheet member 20: polypropylene (PP)
(2) material for an insulator 40: urethane
(3) diameter of a hole H: 2 mm
(4) interval a of holes H: 40 mm
(5) interval β of holes H: 30 mm
(6) height of projections 13 and 14: 5.5 mm
(7) diameter of end portion of projections 13 and 14: 2 mm
(8) diameter of base portion (opening) of projections 13 and 14: 7 mm
(9) interval of projections 13 and 14: 11 mm
(10) thickness of thin panels 11 and 12: 0.5 mm
(11) thickness of a sheet member 20: 5.5 mm
(12) thickness of flooring 30: 2 mm
(13) thickness of an insulator 40: 20 mm
[0036] Description is given of sound absorption by the floor sheet assembly 1, which satisfies the conditions described above, with reference to FIG. ...
PUM
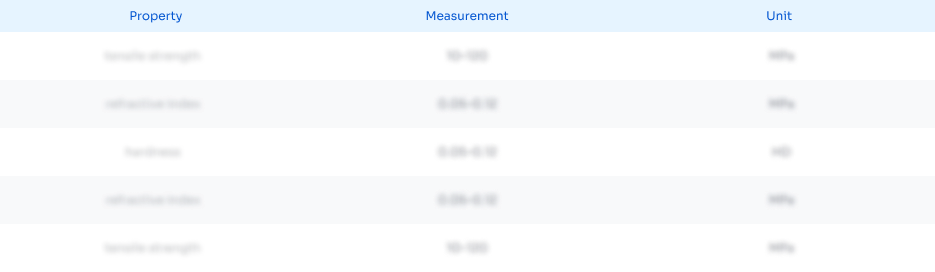
Abstract
Description
Claims
Application Information

- R&D Engineer
- R&D Manager
- IP Professional
- Industry Leading Data Capabilities
- Powerful AI technology
- Patent DNA Extraction
Browse by: Latest US Patents, China's latest patents, Technical Efficacy Thesaurus, Application Domain, Technology Topic, Popular Technical Reports.
© 2024 PatSnap. All rights reserved.Legal|Privacy policy|Modern Slavery Act Transparency Statement|Sitemap|About US| Contact US: help@patsnap.com