Compliant brush shroud assembly for gas turbine engine compressors
a gas turbine engine and compressor technology, applied in the direction of leakage prevention, air transportation, jet propulsion plants, etc., can solve the problems of reducing the compressor performance, reducing the maintenance cost, degrading the compressor performance, etc., and achieves the effects of easy maintenance, low cost, and easy manufacturing
- Summary
- Abstract
- Description
- Claims
- Application Information
AI Technical Summary
Benefits of technology
Problems solved by technology
Method used
Image
Examples
example 1
[0039] Low speed incursion tests were conducted with a variety of both flared and unflared bristle strips. Also, several samples were fabricated with a low bristle angle of about 10°, to minimize the interference of the bristles with the rotating blade tips. The bristle interference proportional to l(1−Cos θ), where l is the bristle length and θ bristle angle. By lowering the angle, the bristle pack radial stiffness was also increased. In the extreme case of 0° bristle angle, there will be no ‘bristle suck down’. However, bristle pack may tend to buckle instead of bending and increase the severity of the impact damage.
TABLE 1Bristle Characteristics of Low Speed Incursion TestsFlared (F)Estimated RadialUnflaredStiffnessSample #Bristle AngleBristle Density(U)Psi / mil145°1500 / inchU.33245°1500 / inchF.33335°1300 / inchU.54435°1300 / inchF.54525°1100 / inchU1.35625°1100 / inchF1.35710°1100 / inchF10.88810°1500 / inchF13.99
[0040] The ID of the samples was ED machined to 11″, same as the rotor OD. Duri...
PUM
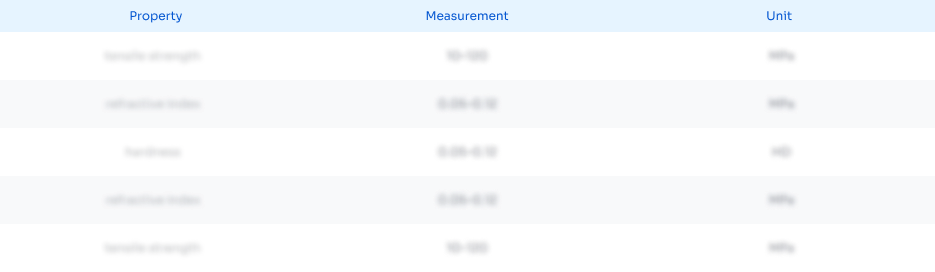
Abstract
Description
Claims
Application Information

- R&D
- Intellectual Property
- Life Sciences
- Materials
- Tech Scout
- Unparalleled Data Quality
- Higher Quality Content
- 60% Fewer Hallucinations
Browse by: Latest US Patents, China's latest patents, Technical Efficacy Thesaurus, Application Domain, Technology Topic, Popular Technical Reports.
© 2025 PatSnap. All rights reserved.Legal|Privacy policy|Modern Slavery Act Transparency Statement|Sitemap|About US| Contact US: help@patsnap.com