Manufacturing method of wavelength filter
- Summary
- Abstract
- Description
- Claims
- Application Information
AI Technical Summary
Benefits of technology
Problems solved by technology
Method used
Image
Examples
Embodiment Construction
[0045] The following detailed description will present a preferred embodiment of the invention in reference to the accompanying drawings.
[0046]FIG. 2A to FIG. 2E diagrammatically illustrate one embodiment of a manufacturing procedure of a mold for use with the manufacture of a wavelength filter according to the present invention.
[0047] The mold has a concavo-convex shape opposite to the concavo-convex shape of a desired polymer fine pattern, and is preferably made from metallic materials with high strength, e.g., Nickel (Ni).
[0048] As shown in FIG. 2A, a polymer layer 110 is formed on a silicon substrate 100 by a spraying or spin coating method. In particular, the polymer layer 110 is deposited on the substrate 100 to a thickness of several micrometers.
[0049] As for the polymer layer 110 materials normally sensitive to electron beams such as PMMA (polymethylmethacrylate) are used.
[0050] Therefore, when the electron beams are irradiated over a certain part of the polymer layer, ...
PUM
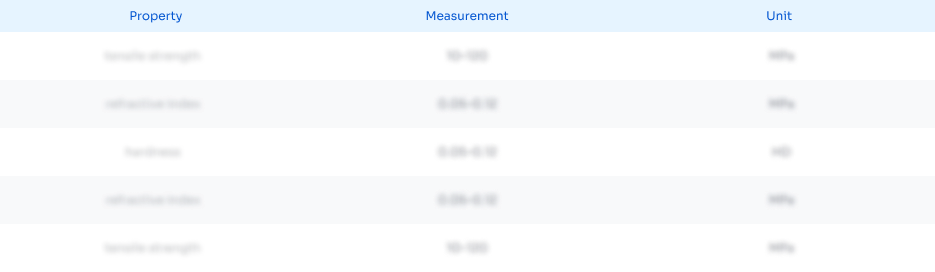
Abstract
Description
Claims
Application Information

- R&D
- Intellectual Property
- Life Sciences
- Materials
- Tech Scout
- Unparalleled Data Quality
- Higher Quality Content
- 60% Fewer Hallucinations
Browse by: Latest US Patents, China's latest patents, Technical Efficacy Thesaurus, Application Domain, Technology Topic, Popular Technical Reports.
© 2025 PatSnap. All rights reserved.Legal|Privacy policy|Modern Slavery Act Transparency Statement|Sitemap|About US| Contact US: help@patsnap.com