Light source detection and categorization system for automatic vehicle exterior light control and method of manufacturing
a technology for automatic vehicle exterior light control and light source detection, applied in the direction of optical radiation measurement, photometry using electric radiation detectors, instruments, etc., can solve the problems of pixel non-uniformity, pixel sensitivity variation, and difficulty in adjusting the sensitivity of the pixel, so as to simplify the manufacturing method and reduce the cost. , the effect of facilitating the replacement of the lens system
- Summary
- Abstract
- Description
- Claims
- Application Information
AI Technical Summary
Benefits of technology
Problems solved by technology
Method used
Image
Examples
example 1a
[0098] The optical system of this example is constructed as depicted and described with regard to FIG. 3 and results in a sharply focused optical system. The pixel array is a complementary metal-oxide silicon (CMOS) active pixel array comprising a 64 pixels horizontal×80 pixels vertical array of 30 μm, photogate pixels. The thickness of the encapsulate block (dimension C as shown in FIG. 3), measured from the top surface of the pixel array to the top surface of the encapsulate block, is 3.75 mm. Each lens system has a diameter of 4.4 mm, a radius of curvature of 2.6 mm and a conic constant of −0.4. The thickness of the lens system assembly (dimension A in FIG. 3) is 3.0 mm. The centers of the individual lens systems are spaced by 1.44 mm; each lens system is truncated on one side to place the center-to-center distance of the lens systems at the desired distance to form the lens system assembly. Sub windows of 60 pixels horizontally×26 pixels vertically are chosen for image acquisiti...
example 1b
[0102] In order to achieve accurate digital sampling of the imaged scene in accordance with the present invention, the optical system of example 1a should be modified to have a spatial frequency cutoff that is less than, or equal to, the Nyquist frequency limit of the pixel array. This is achieved in accordance with the present invention by modifying the thickness of the encapsulate block to produce a more “blurred” image with a lower spatial frequency cutoff. FIG. 7 depicts the MTF plot of the optical system described in example 1a modified with the thickness of the encapsulate block (dimension C as shown in FIG. 3) reduced to 3.65 mm. This reduction in block height limits the absolute spatial frequency cutoff of the optical system to approximately 17 cycles / mm, shown at reference 705 in FIG. 7, roughly the same as the limit of the pixel array of 16.67 cycles / mm.
[0103]FIG. 7 also depicts plots of modulation transfer functions, in dashed and dotted lines, of alternated embodiments ...
example 2
[0167] The optical system of this example of the present invention employs a high resolution pixel array to achieve a wider field of view and greater discrimination of distinct light sources. A 176 pixels horizontal×144 pixels vertical pixel array (commonly referred to as quarter-common image format (QCIF)) containing 15 μm pixels is used. The configuration of the optical system is as shown in FIG. 3. Lens systems with a diameter of 3.5 mm, a radius of curvature of 2.15 mm and a conic constant of −0.4 are used. The lens system assembly is 3.0 mm thick (dimension A as shown in FIG. 3), the adhesive layer is 0.25 mm thick (dimension B as shown in FIG. 3) and the encapsulate block is 2.5 mm thick (dimension C as shown in FIG. 3). Sub-windows of 120 pixels horizontal by 50 pixels vertical on each half of the pixel array are used for a field of view of approximately 29° horizontal×12° vertical (approx. 0.241 / pixel). FIG. 36 depicts a MTF plot of the optical system of this example using a...
PUM
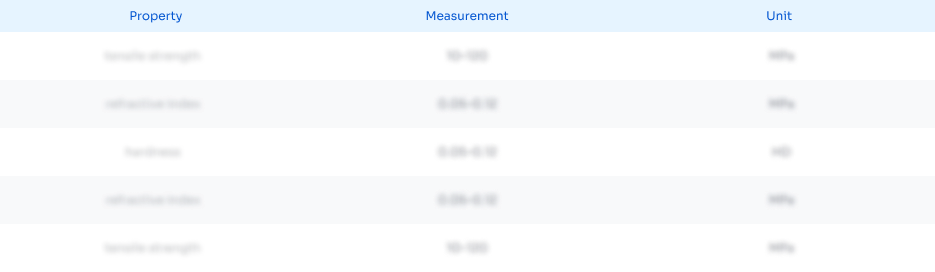
Abstract
Description
Claims
Application Information

- R&D
- Intellectual Property
- Life Sciences
- Materials
- Tech Scout
- Unparalleled Data Quality
- Higher Quality Content
- 60% Fewer Hallucinations
Browse by: Latest US Patents, China's latest patents, Technical Efficacy Thesaurus, Application Domain, Technology Topic, Popular Technical Reports.
© 2025 PatSnap. All rights reserved.Legal|Privacy policy|Modern Slavery Act Transparency Statement|Sitemap|About US| Contact US: help@patsnap.com