Interface and method of interfacing between a parametric modelling unit and a polygon based rendering system
- Summary
- Abstract
- Description
- Claims
- Application Information
AI Technical Summary
Problems solved by technology
Method used
Image
Examples
case 1
[0174]
[0175] Starting with the numerator / denominator `contents` we have 15 lim e 0 1 e B _ Delta= lim e 0 [ e 2e 1 0] Q P _ left -column xyz P 00 w - P _ 00 xyz [ e 2e 1 0] QP left - column w = [0 0 1 0] Q P _ left -column xyz P 00 w - P _ 00 xyz [0 0 1 0] QP left -column w = [ - 3 3 0 0] P _ left -column xyz P 00 w - P _ 00 xyz [ - 33 0 0] QP left - column w =3 ((P _ 10 xyz P _ 00 xyz )P 00 w-P _ 00 xyz ( P 10 w - P 00 w) ) =3 (P 10 xyz P 00 w-P _ 00 xyz P 10 w )
[0176] The limit clearly exists and will be non-zero if and only if {overscore (P)}.sub.10.sub..sub.xyzP.sub.00w.noteq.P.sub.00xyzP.sub.10w. If this condition holds then a tangent vector in the direction S is given by {overscore (T)}.sub.S1={overscore (P)}.sub.10.sub..sub.xyzP.sub.00w.no-teq.P.sub.00xyzP.sub.10.sub..sub.w. Note that the length of the vector is immaterial at this point.
case 2
[0177]
[0178] if the condition of case 1 is not met, (i.e. {overscore (P)}.sub.10.sub..sub.xyzP.sub.00w.noteq.P.sub.00xzyP.sub.10.sub..sub.w), then the limits of the second case are examined. This gives: 16 lim e 0 1 e 2 B _ Delta( e , 0 ) = lim e 0 1 e (B _ Delta( e , 0 ) )
[0179] Noting that . . . 17 1 e B _ Delta( e , 0 )= [ e 2e 1 0] Q P _ left_column xyz P 00 w - P _ 00 xyz [ e 2e 1 0] QP left_column w = [ e 2e 0 0] Q P _ left_column xyz P 00 w - P _ 00 xyz [ e 2e 0 0] QP left_column w+ [0 0 1 0] Q P _ left_column xyz P 00 w -P _ 00 xyz [0 0 1 0] QP left_column w
[0180] . . . we see that the second part of the sum is the same as the result from case 1, which have assumed to be zero. We thus get 18 lim e 0 1 e 2 B Delta( e , 0 ) = lim e 0 1 e[ e 2e 0 0]Q P _ left column xyz P 00 w - P _ 00 xyz [ e 2e 0 0] QP left_column w = lim e 1 e[ e e 0 0]Q P _ left_column xyz P 00 w - P _ 00 xyz [ e e 0 0] QP left_column w = [0 1 0 0] Q P _ left_column xyz P 00 w - P _ 00 xyz [ 0 1 0 0] QP lef...
case 3
[0183]
[0184] Should both cases 2 and 3 fail, then using a similar argument to these presented, an "S" may be computed from {overscore (T)}.sub.03={overscore (P)}.sub.30.sub..sub.xyzP.sub.00w-{overscore (P)}.sub.00xyz{overscore (P)}.sub.30.sub..sub.w, provided that is non zero.
[0185] Derivation of a Candidate Tangent Vector in the `T` Direction:
[0186] This follows exactly the same reasoning as for the "S" tangent, and so will not be discussed here.
[0187] Derivation of a Candidate Tangent Vector in the `diagonal` Direction:
[0188] If the {overscore (T)}.sub.S.alpha. and {overscore (T)}.sub.T.beta. candidate tangent are linearly dependent then by themselves they are not suitable for generating the normal vector. In this case it is necessary to manufacture another tangent candidate, which will be referred to as the `diagonal` tangent candidate.
[0189] For the purposes of the preferred embodiment, it is assumed that at least one of {overscore (T)}.sub.S.alpha. or {overscore (T)}.sub.T.beta...
PUM
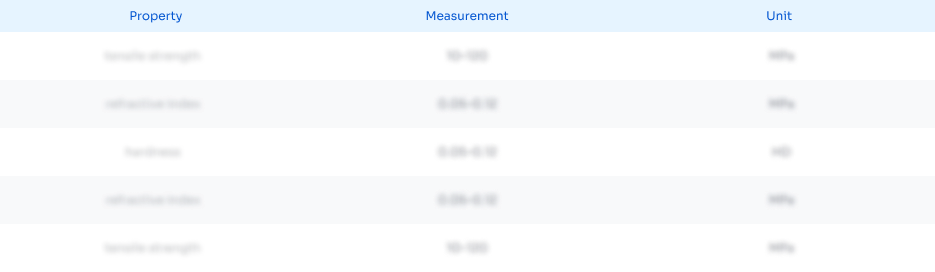
Abstract
Description
Claims
Application Information

- R&D
- Intellectual Property
- Life Sciences
- Materials
- Tech Scout
- Unparalleled Data Quality
- Higher Quality Content
- 60% Fewer Hallucinations
Browse by: Latest US Patents, China's latest patents, Technical Efficacy Thesaurus, Application Domain, Technology Topic, Popular Technical Reports.
© 2025 PatSnap. All rights reserved.Legal|Privacy policy|Modern Slavery Act Transparency Statement|Sitemap|About US| Contact US: help@patsnap.com