Process and apparatus of combustion for reduction of nitrogen oxide emissions
a technology of nitrogen oxide and process, which is applied in the direction of indirect carbon-dioxide mitigation, air/fuel supply for combustion, lighting and heating apparatus, etc., can solve the problems of low excess air reducing the available oxygen, scr and sncr systems tend to have extremely high capital and maintenance costs,
- Summary
- Abstract
- Description
- Claims
- Application Information
AI Technical Summary
Problems solved by technology
Method used
Image
Examples
Embodiment Construction
[0081] FIG. 6 illustrates schematically the implementation of a process for fuel combustion in a single burner end fired furnace 600. The oscillating flame 610 is illustrated with the low and high flames represented. The post combustion oxidant is injected at a one or more locations represented by the arrows 620. The post combustion oxidant injection locations are selected to be where the injected oxidant will not interact with the oscillating combustion and where the flue gas temperature is the lowest in the furnace. These locations in the furnace are generally along the back wall and along the exhaust gas path on the side of the furnace. The furnace 600 of FIG. 6 may be any known end fired furnace, such as a glass furnace or steel making furnace.
[0082] FIG. 7 illustrates schematically the implementation of a process for fuel combustion in a multiple burner, cross fired furnace 700. The plurality of oscillating flames 710 are illustrated on both sides of the furnace with the low fl...
PUM
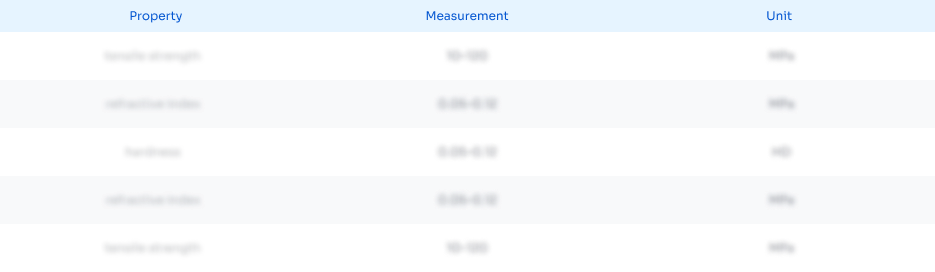
Abstract
Description
Claims
Application Information

- R&D
- Intellectual Property
- Life Sciences
- Materials
- Tech Scout
- Unparalleled Data Quality
- Higher Quality Content
- 60% Fewer Hallucinations
Browse by: Latest US Patents, China's latest patents, Technical Efficacy Thesaurus, Application Domain, Technology Topic, Popular Technical Reports.
© 2025 PatSnap. All rights reserved.Legal|Privacy policy|Modern Slavery Act Transparency Statement|Sitemap|About US| Contact US: help@patsnap.com