Catalytic cracking process of petroleum hydrocarbons
a petroleum hydrocarbon and cracking technology, applied in the direction of catalytic cracking, catalytic naphtha reforming, chemistry apparatus and processes, etc., can solve the problems of untiring research and study by refiners, product distribution and product properties cannot be improved by means of optimizing operation variables, and the cost of both equipment reconstruction and unit construction is increased significantly
- Summary
- Abstract
- Description
- Claims
- Application Information
AI Technical Summary
Benefits of technology
Problems solved by technology
Method used
Image
Examples
example 2
[0076] The present example shows test results obtained by using the process provided in the present invention when a liquefied petroleum gas is produced as main object product.
[0077] Main steps of the test are as follows The feedstock shown in Table 1 was heated via a preheating furnace, then fed to the inner tube of the tube-in-tube riser reactor to contact the regenerated catalyst flowing from the regenerator and lifted with a pre-lifting media. The light oil (gasoline diesel oil) with a distillation range less than 350.degree. C. produced in the present unit was fed into the annular space between the inner and outer tubes to contact the regenerated catalyst therein. Both the reaction stream from the inner tube and the reaction stream from the annular space moved up along vessel wall respectively, mixed with each other in the confluence tube to continue the reaction, and then entered a disengager. In the disengager, the hydrocarbon product stream was separated from the spent catal...
example 3
[0079] The present example shows test results obtained by using the process provided in the present invention when gasoline is produced as main object product.
[0080] The main steps of the test are as follows. The feedstock shown in Table 1 and the recycled oil produced in the present unit were mixed, then the mixed oil was heated via a preheating furnace and fed to the inner tube of the tube-in-tube riser reactor to contact the regenerated catalyst flowing from the regenerator and lifted with a pre-lifting media. Coker gasoline (with a density of 0.7316 g / cm.sup.3, RON=58.8, MON=65.4, an olefin content of 37.49% by weight) was fed to the annular space between the inner and outer tubes to contact the regenerated catalyst therein. Both the reaction stream in the inner tube and the reaction stream in the annular space moved up along vessel wall respectively, mixed with each other in the confluence tube to continue the reaction, and then entered a disengager. In the disengager, the hydr...
example 4
[0082] The present example shows test results obtained by using the process provided in the present invention when diesel oil is produced as main object product.
[0083] Main steps of test are as follows. As shown in FIG. 7, the feedstock shown in Table I was mixed with the recycled oil of the present unit, the mixed oil was heated via a preheating furnace and fed to the inner tube of the tube-in-tube riser reactor to contact the mixed catalyst from catalyst blending vessel 16 in which the regenerated catalyst and the spent catalyst were mixed. The coker diesel oil (with a density of 0.8520 g / cm.sup.5, a sulfur content of 8225 ppm, and a nitrogen content of 5018 ppm, and a cetane number of 47) was fed to the annular space between the inner and outer tubes to contact the mixed catalyst therein. Both the reaction stream in the inner tube and the reaction stream in the annular space moved up along vessel wall respectively, then mixed with each other in the confluence tube to continue the...
PUM
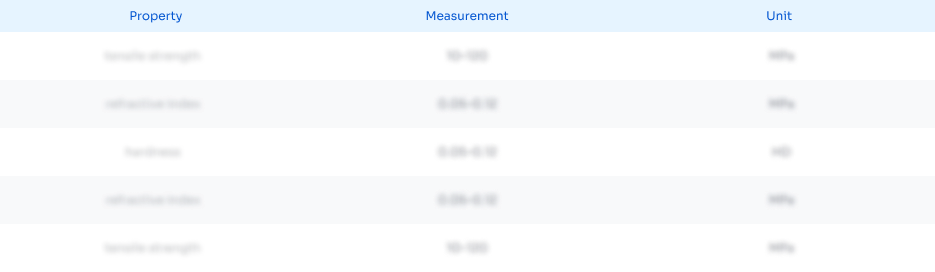
Abstract
Description
Claims
Application Information

- R&D
- Intellectual Property
- Life Sciences
- Materials
- Tech Scout
- Unparalleled Data Quality
- Higher Quality Content
- 60% Fewer Hallucinations
Browse by: Latest US Patents, China's latest patents, Technical Efficacy Thesaurus, Application Domain, Technology Topic, Popular Technical Reports.
© 2025 PatSnap. All rights reserved.Legal|Privacy policy|Modern Slavery Act Transparency Statement|Sitemap|About US| Contact US: help@patsnap.com