Glulam wood beams and method of making same
a technology of glue and wood beams, applied in the field of wood beams, can solve the problems of difficult glueing of planks, difficult to reach objects, and tendency to change shape upon drying, and achieve the effect of increasing mechanical stability
- Summary
- Abstract
- Description
- Claims
- Application Information
AI Technical Summary
Benefits of technology
Problems solved by technology
Method used
Image
Examples
example 1
Precomposition of individual strips panels
[0060] A. Individual strips
[0061] A strip of a width of twelve inches (273 mm) may be obtained by assembling three planks with three two by four (2".times.4") planks. The sides of the two planks located at the lateral ends of the strips form sharp edges (devoided of flash) with the top and the bottom of the planks.
[0062] Panels
[0063] A width of thirteen inches (289 mm) may be obtained by assembling planks into panels that are then cut at the appropriate position. For example, the panel may be composed of one 2".times.4" plank, three 2".times.3" planks, etc. The cutting of the panel into strips is accomplished by cutting the 2".times.4": pls at a position X.sub.0 and X.sub.1 according to the method described above to obtain a strip with a width of thirteen inches.
example 2
Assembly of beams of various width using planks of various width
[0064] The following table presents the width of beams that can be obtained using strips comprising 2".times.3", 2".times.4" and 2".times.6" planks. The table also contains information on the loss of material during the manufacture of the beams. Also shown is the ratio of original wood material necessary to produce one metre cubed of finished products as well as the width of beams available on the market.
1TABLE Finished product ratio starting beam dimension Lost of material material (m.sup.3 beam dimension (inches and mm) of (m.sup.3 finished product for starting material (inches) available the instant Recurring 1 m.sup.3 of starting material) for 1 m.sup.3 finished commercially invention of beams Length Cutting Planing product 2 1 / 2 2 1 / 8 54 MM 1 / 4 strip B 0,9 0,685 0,948 1,711 3 3 1 / 8 3 1 / 8 79,3 MM 1 / 3 strip A 0,9 0,75 0,953 1,555 3 1 / 2 3 1 / 2 88,9 MM 1 / 3 strip E 0,9 0,785 0,959 1.555 4 1 / 8 105 MM strip D 5 4 7 / 8 122,5...
example 3
Examples of beams comprising flash according to the instant invention
[0072] The models of beams described below will be better understood by referring to FIGS. 10-15.
[0073] A. In the beam of FIG. 10, the central part 101 comprises individual squared planks having a width equal to the width of the strip of the top and bottom strips of the beam.
[0074] B. The beam of FIG. 11 is formed by two strips 111 vertically adhered and in which the lateral joints of the central part are out of line.
[0075] C. The beam illustrated in FIG. 12 is composed of three strips 121 vertically adhered and in which the later joints of the central part are substantally co-linear.
[0076] D. The beam illustrated in FIG. 13 is composed of three strips 131 vertically adhered and in which the lateral joints forming the central part are co-linear. The top and the bottom part of the beam are formed by strips devoided of flash and being optionally reinforced with fiberglass, carbon or airmide bands. In addition, the wi...
PUM
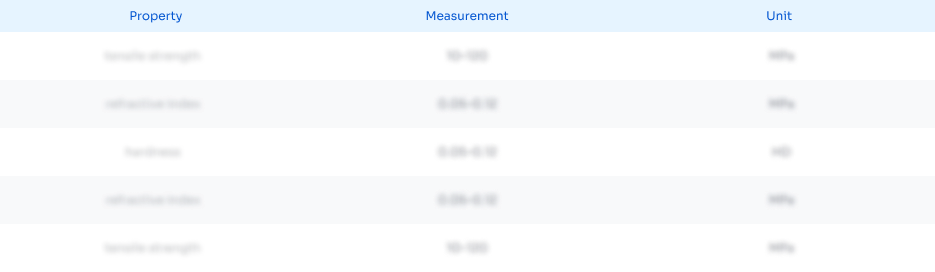
Abstract
Description
Claims
Application Information

- R&D
- Intellectual Property
- Life Sciences
- Materials
- Tech Scout
- Unparalleled Data Quality
- Higher Quality Content
- 60% Fewer Hallucinations
Browse by: Latest US Patents, China's latest patents, Technical Efficacy Thesaurus, Application Domain, Technology Topic, Popular Technical Reports.
© 2025 PatSnap. All rights reserved.Legal|Privacy policy|Modern Slavery Act Transparency Statement|Sitemap|About US| Contact US: help@patsnap.com