Mooring systems with active force reacting systems and passive damping
a technology of active force and reacting system, applied in vessel construction, special-purpose vessels, transportation and packaging, etc., can solve the problems of increasing damping, increasing the damping of spring-like systems, and insufficient damping of vessels moving through water
- Summary
- Abstract
- Description
- Claims
- Application Information
AI Technical Summary
Benefits of technology
Problems solved by technology
Method used
Image
Examples
Embodiment Construction
[0045] Soft yoke mooring systems rely on restoring forces generated by linkages connected to pendular weights. As a result, the restoring force is sinusoidal with displacement as shown in curve "A" of FIG. 1. FIG. 1 is a restoring force versus displacement diagram showing restoring force as a function of displacement of a yoke from a vessel. The neutral or quiescent point is the position of the yoke when the vessel is at rest. Because the restoring force for displacements about the neutral point is so low (essentially zero), soft yoke systems i.e. pendular yoke systems as illustrated by curve A require relatively large displacements to generate the required restoring force and absorb kinetic energy. This characteristic requires large linkages and weights which implies high cost of steel structures. Because there is little damping, peak compression loads toward the tower of a magnitude of 5 / 9 of peak tension loads away from the tower are seen. For example, the compression restoring f...
PUM
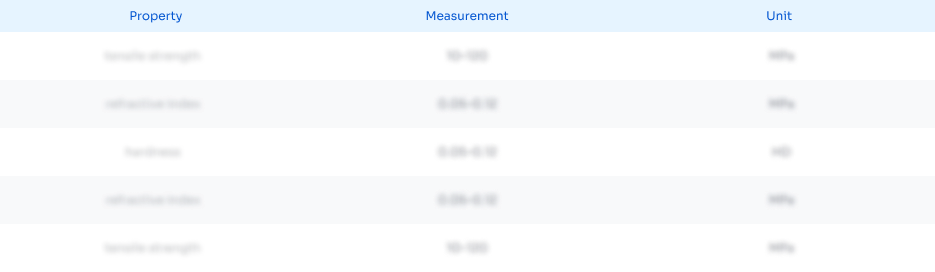
Abstract
Description
Claims
Application Information

- R&D
- Intellectual Property
- Life Sciences
- Materials
- Tech Scout
- Unparalleled Data Quality
- Higher Quality Content
- 60% Fewer Hallucinations
Browse by: Latest US Patents, China's latest patents, Technical Efficacy Thesaurus, Application Domain, Technology Topic, Popular Technical Reports.
© 2025 PatSnap. All rights reserved.Legal|Privacy policy|Modern Slavery Act Transparency Statement|Sitemap|About US| Contact US: help@patsnap.com