Zinc-aluminium alloy wire, and its manufacturing method and use
A technology of zinc-aluminum alloy wire and its manufacturing method, which is applied in the direction of manufacturing tools, metal processing equipment, forging/pressing/hammer devices, etc., can solve problems such as difficulty in ensuring uniform structure, increased plastic deformation resistance, and increased segregation phenomenon, and achieves The effect of cost saving, good performance and simplified process
- Summary
- Abstract
- Description
- Claims
- Application Information
AI Technical Summary
Problems solved by technology
Method used
Image
Examples
example 1
[0021] Zinc-aluminum alloy, wherein the atomic percentage of metal aluminum in the alloy is 55%. First, 663g of zinc ingots containing 99.99% of zinc and 337g of aluminum ingots containing 99.7% of aluminum are placed in a vacuum induction melting furnace to melt into ZnAl 55 For alloy ingots, the melting temperature is 650°C, the dummy speed is 50-80mm / min, the cutting size is Φ18-30mm, and the lubricant is high-quality carbon ink. Then put the finished alloy ingot into a rotary forging machine for rotary forging to make its composition uniform. The heating temperature of the rotary forging is 400°C, the forging temperature is 400°C, and the final forged size is Φ8-15mm. Then put the forged alloy wire into the drawing equipment for medium-temperature drawing. At this time, the heating temperature is 350°C, the drawing temperature is 300°C, and the finally drawn alloy wire has a specification of Φ2.5-4mm.
Embodiment 2
[0023] Zinc-aluminum alloy, wherein the atomic percentage of metal aluminum in the alloy is 50%. First, 663g of zinc ingots containing 99.99% of zinc and 337g of aluminum ingots containing 99.7% of aluminum are placed in a vacuum induction melting furnace to melt into ZnAl 50 For alloy ingots, the melting temperature is 500°C, the dummy speed is 50-80mm / min, the cutting size is Φ18-30mm, and the lubricant is high-quality carbon ink. Then put the finished alloy ingot into a rotary forging machine for rotary forging to make its composition uniform. The heating temperature of the rotary forging is 350°C, the forging temperature is 350°C, and the final forged size is Φ8-15mm. Then put the forged alloy wire into the drawing equipment for medium-temperature drawing. At this time, the heating temperature is 300°C, the drawing temperature is 260°C, and the finally drawn alloy wire has a specification of Φ2.5-4mm.
Embodiment 3
[0025] Zinc-aluminum alloy, wherein the weight percentage of metal aluminum in the alloy is 45%. First, 663g of zinc ingots containing 99.99% of zinc and 337g of aluminum ingots containing 99.7% of aluminum are placed in a vacuum induction melting furnace to melt into ZnAl 45 For alloy ingots, the melting temperature is 450°C, the dummy speed is 50-80mm / min, the cutting size is Φ18-30mm, and the lubricant is high-quality carbon ink. Then put the finished alloy ingot into the rotary forging machine for rotary forging to make its composition uniform. The heating temperature of the rotary forging is 300°C, the forging temperature is 300°C, and the final forged size is Φ8-15mm. Then put the forged alloy wire into the drawing equipment for medium-temperature drawing. At this time, the heating temperature is 250°C, the drawing temperature is 250°C, and the finally drawn alloy wire has a specification of Φ2.5-4mm.
PUM
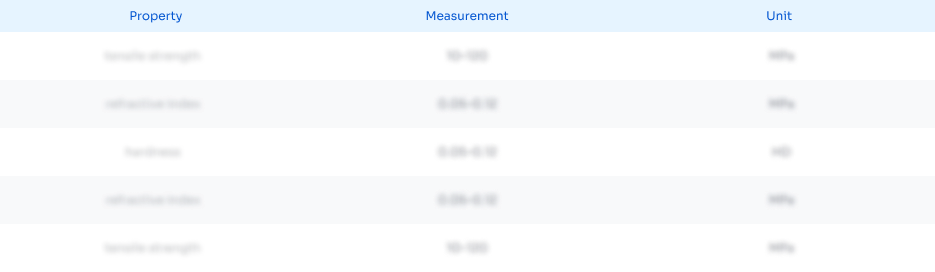
Abstract
Description
Claims
Application Information

- R&D
- Intellectual Property
- Life Sciences
- Materials
- Tech Scout
- Unparalleled Data Quality
- Higher Quality Content
- 60% Fewer Hallucinations
Browse by: Latest US Patents, China's latest patents, Technical Efficacy Thesaurus, Application Domain, Technology Topic, Popular Technical Reports.
© 2025 PatSnap. All rights reserved.Legal|Privacy policy|Modern Slavery Act Transparency Statement|Sitemap|About US| Contact US: help@patsnap.com