Method of decomposing thermoset epoxy resin and its composite material
A technology of epoxy resin and composite materials, applied in the direction of plastic recycling, recycling technology, etc., can solve the problem that reinforcing fibers cannot be separated and recycled
- Summary
- Abstract
- Description
- Claims
- Application Information
AI Technical Summary
Problems solved by technology
Method used
Examples
specific Embodiment approach 1
[0006] Specific embodiment one: the thermosetting epoxy resin of this embodiment is decomposed by the following steps: (1) add thermosetting epoxy resin and decomposition solution to the reaction kettle in the ratio of 10~25g: 100mL; (2) put the reaction kettle into Decompose in a salt bath furnace at a temperature of 280° C. to 350° C. for 1 to 2 hours to complete the decomposition of the thermosetting epoxy resin; wherein the decomposition liquid is a partially hydrogenated aromatic compound.
[0007] In this embodiment, the whole process is pollution-free, and the equipment used is simple and easy to operate. More than 95% of the decomposition products of thermosetting epoxy resins are benzene homologues and phenol homologues by using infrared spectroscopy and gas chromatography-mass spectrometry on-line analysis; according to the principle of chemical similarity and compatibility, thermosetting epoxy resins are completely soluble in partially hydrogenated aromatics after de...
specific Embodiment approach 2
[0008] Specific embodiment two: the difference between this embodiment and specific embodiment one is: in step (1), thermosetting epoxy resin and decomposition solution are added to the reactor in the ratio of 15-22g: 100mL. Other steps are the same as those in Embodiment 1.
specific Embodiment approach 3
[0009] Specific embodiment three: the difference between this embodiment and specific embodiment one is: in step (1), thermosetting epoxy resin and decomposition solution are added to the reactor in the ratio of 20g: 100mL. Other steps are the same as those in Embodiment 1.
PUM
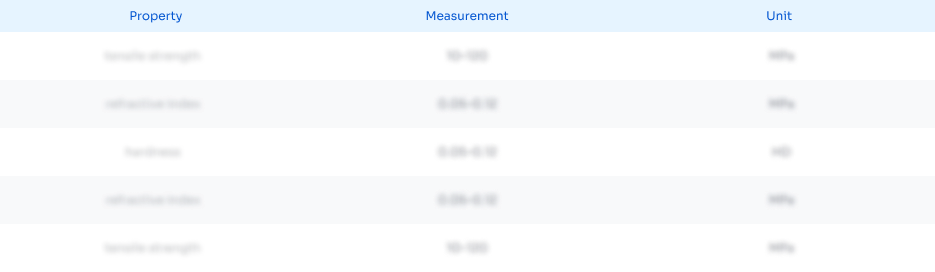
Abstract
Description
Claims
Application Information

- R&D
- Intellectual Property
- Life Sciences
- Materials
- Tech Scout
- Unparalleled Data Quality
- Higher Quality Content
- 60% Fewer Hallucinations
Browse by: Latest US Patents, China's latest patents, Technical Efficacy Thesaurus, Application Domain, Technology Topic, Popular Technical Reports.
© 2025 PatSnap. All rights reserved.Legal|Privacy policy|Modern Slavery Act Transparency Statement|Sitemap|About US| Contact US: help@patsnap.com