Zero discharging system for cement kiln clinker cooling machine waste gas
A cooling machine, cement kiln technology, applied in the direction of furnace cooling, furnace, lighting and heating equipment, etc., can solve the problems of high dust removal equipment requirements, high operating costs, environmental pollution, etc., to eliminate exhaust pollution, reduce energy consumption and Effect of investment, heat up
- Summary
- Abstract
- Description
- Claims
- Application Information
AI Technical Summary
Problems solved by technology
Method used
Image
Examples
Embodiment
[0016] Taking the 2500t / d clinker firing system as an example, the cement clinker with a temperature of 1400°C coming out of the rotary kiln 22 enters the grate cooler 13 and forms a material layer with a certain thickness on the grate cooling bed that moves toward the cold end. There are 12 cooling fans under the bed, the parameters of which are shown in the table below. The air blown by the cooling fan passes through the material layer and is heated while cooling the clinker. Part of the heated hot air is used as combustion air for the rotary kiln (secondary air) and calciner (tertiary air), and all or part of the hot air is used as waste heat. Boiler 16 heat sources. The hot air used as the heat source of the waste heat boiler 16 is connected to the waste heat boiler 16 at the kiln head through the pre-dust collector 15, and the waste gas exiting the waste heat boiler 16 at the kiln head and / or the grate cooler 13 is connected to the inlet of the dust collector 18 through t...
PUM
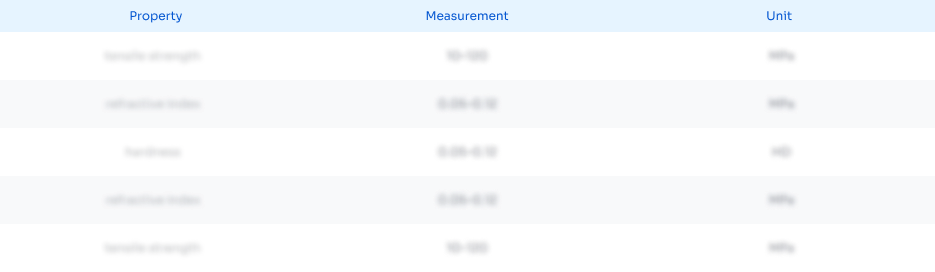
Abstract
Description
Claims
Application Information

- Generate Ideas
- Intellectual Property
- Life Sciences
- Materials
- Tech Scout
- Unparalleled Data Quality
- Higher Quality Content
- 60% Fewer Hallucinations
Browse by: Latest US Patents, China's latest patents, Technical Efficacy Thesaurus, Application Domain, Technology Topic, Popular Technical Reports.
© 2025 PatSnap. All rights reserved.Legal|Privacy policy|Modern Slavery Act Transparency Statement|Sitemap|About US| Contact US: help@patsnap.com