Silicon mullite red brick for large cement kiln and its producing method
A silicon molybdenum brick and a manufacturing method technology, applied in the field of refractory materials, can solve the problems of short service life and high cost, and achieve the effects of low cost, long operation period and obvious heat insulation effect
- Summary
- Abstract
- Description
- Claims
- Application Information
AI Technical Summary
Problems solved by technology
Method used
Examples
Embodiment 1
[0015] Embodiment 1, large-scale cement kiln uses silicon Mo red brick, the weight proportion of each component is:
[0016] Super Bauxite Aggregate 0-6mm Al 2 o 3 ≥85% 50%
[0017] Silicon carbide ≤0.088mm SiC≥92% 10%
[0018] Fused white corundum powder ≤0.088mm Al 2 o 3 ≥98% 20%
[0019] Selected andalusite powder ≤0.088mm Al 2 o 3 ≥58% 15%
[0020] Bound clay ≤0.088mm Al 2 o 3 ≥38% 5%
[0021] Plus:
[0022] Yellow dextrin 0.3%
[0023] Methylcellulose 0.5%
[0024] water 4%
[0025] Mix the raw materials in the above proportions, make mud in a kneader, and shape it under a pressure of 630KN. The shaped bricks are sintered in a tunnel kiln at 1500 ° C ± 10.
Embodiment 2
[0026] Embodiment 2, with reference to Example 1, the weight proportion of each component is:
[0027] Super Bauxite Aggregate 0-6mm Al 2 o 3 ≥85% 56%
[0028] Silicon carbide ≤0.088mm SiC≥92% 20%
[0029] Fused white corundum powder ≤0.088mm Al 2 o 3 ≥98% 8%
[0030] Selected andalusite powder ≤0.088mm Al 2 o 3 ≥58% 10%
[0031] Bound clay ≤0.088mm Al 2 o 3 ≥38% 6%
[0032] Plus:
[0033] Yellow dextrin 0.5%
[0034] Methylcellulose 0.6%
[0035] water 3%
Embodiment 3
[0036] Embodiment 3, with reference to Example 1, the weight proportion of each component is:
[0037] Super Bauxite Aggregate 0-6mm Al 2 o 3 ≥85% 60%
[0038] Silicon carbide ≤0.088mm SiC≥92% 11%
[0039] Fused white corundum powder ≤0.088mm Al 2 o 3 ≥98% 10%
[0040] Selected andalusite powder ≤0.088mm Al 2 o 3 ≥58% 12%
[0041] Bound clay ≤0.088mm Al 2 o 3 ≥38% 7%
[0042] Plus:
[0043] Yellow Dextrin 0.6%
[0044] Methylcellulose 0.3%
[0045] water 5%
PUM
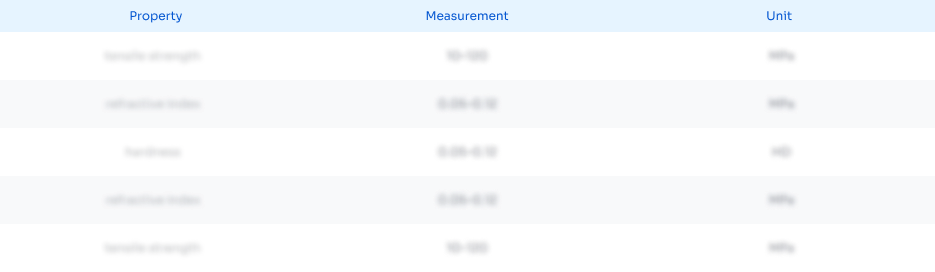
Abstract
Description
Claims
Application Information

- R&D Engineer
- R&D Manager
- IP Professional
- Industry Leading Data Capabilities
- Powerful AI technology
- Patent DNA Extraction
Browse by: Latest US Patents, China's latest patents, Technical Efficacy Thesaurus, Application Domain, Technology Topic, Popular Technical Reports.
© 2024 PatSnap. All rights reserved.Legal|Privacy policy|Modern Slavery Act Transparency Statement|Sitemap|About US| Contact US: help@patsnap.com