Rolling rounder for rolling steel bar
A chamfering and rolling technology, which is applied in the field of steel bar chamfering and rolling full circle devices, can solve problems such as waste products, large deformation of steel bar joints, quality and strength of steel wire heads, etc.
- Summary
- Abstract
- Description
- Claims
- Application Information
AI Technical Summary
Problems solved by technology
Method used
Image
Examples
Embodiment
[0029] Embodiment: See accompanying drawing 2, accompanying drawing 4 and accompanying drawing 9, a kind of helical tooth rolling steel wire end equipment, the chamfering and rounding device that the present invention relates to at the front part and the helical tooth rolling at the rear side The supporting connection of the steel wire head device is formed.
[0030] Referring to accompanying drawings 2, 3, 6 and 9, the specific structure of the chamfering and rounding mechanism is as follows: it includes four chamfering and rounding mechanisms uniformly distributed in the circumferential direction around the central axis of rolling rotation. Circular eccentric shaft 27, each chamfered full-circle eccentric shaft 27 is composed of at least a chamfered eccentric section 46 at the front, a central main shaft section and a rear full-circle eccentric section 47 in the axial direction, wherein the chamfered eccentric section 46 The eccentric phase difference with the full circle ec...
PUM
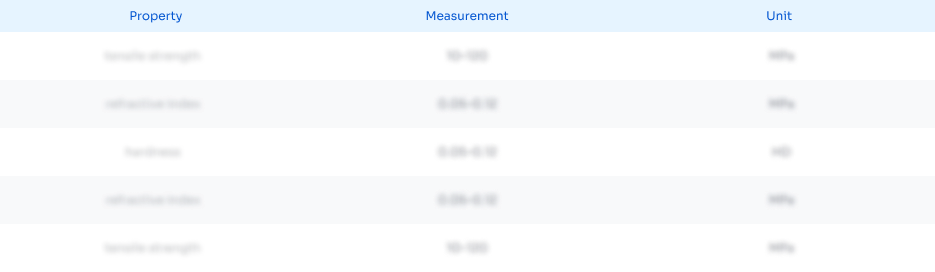
Abstract
Description
Claims
Application Information

- Generate Ideas
- Intellectual Property
- Life Sciences
- Materials
- Tech Scout
- Unparalleled Data Quality
- Higher Quality Content
- 60% Fewer Hallucinations
Browse by: Latest US Patents, China's latest patents, Technical Efficacy Thesaurus, Application Domain, Technology Topic, Popular Technical Reports.
© 2025 PatSnap. All rights reserved.Legal|Privacy policy|Modern Slavery Act Transparency Statement|Sitemap|About US| Contact US: help@patsnap.com