Method and device for improving straight line degree measurement sensitivity
A measurement device and sensitivity technology, applied in the field of photoelectric detection, can solve problems such as difficulty in meeting high precision and ultra-high precision, and achieve the effects of increasing anti-interference ability and stability, improving measurement sensitivity, and improving system measurement sensitivity.
- Summary
- Abstract
- Description
- Claims
- Application Information
AI Technical Summary
Problems solved by technology
Method used
Image
Examples
Embodiment 1
[0027] Embodiment one (as shown in Figure 1):
[0028] The high-sensitivity straightness error measurement system in the system is a high-stable laser beam emitted by the semiconductor laser 1 in the fixed unit 100. After being collimated by the single-mode fiber 2 and the collimator lens 3, it is incident on the polarization beam splitter 4, and the incident light After passing through the polarizing beam splitter 4, it becomes linearly polarized light. The linearly polarized light passes through λ / 4 After wave plate 5, it becomes circularly polarized polarized light. After being reflected by the corner cube prism 11 incident into the mobile unit 200, it passes through λ / 4 After the wave plate, the circularly polarized light becomes linearly polarized again, but its polarization direction is rotated by 90° angle. The light is reflected to another reflector 6 through the polarizing beam splitter, so that the light passes through the corner cube prism 11 of the primary movin...
Embodiment 2
[0037] Embodiment two (as shown in Figure 4):
[0038] The difference from Embodiment 1 is that a reflector 11 is added to the mobile unit 200, and a set of polarization beam splitter 4, λ / 4 wave plate 5, reflector 6, and reflector 13. On the basis of Embodiment 1, the measurement sensitivity of the system is doubled again.
Embodiment 3
[0039] Embodiment three (as shown in Figure 5):
[0040] The difference from Embodiment 1 is that a reflective unit 14 (composed of a retroreflector and a reflector) is used to make the measuring light path pass through the moving target mirror four times to achieve the same sensitivity multiplication effect as Embodiment 2, which is similar to that of Embodiment 2. The difference is to make the system more compact.
PUM
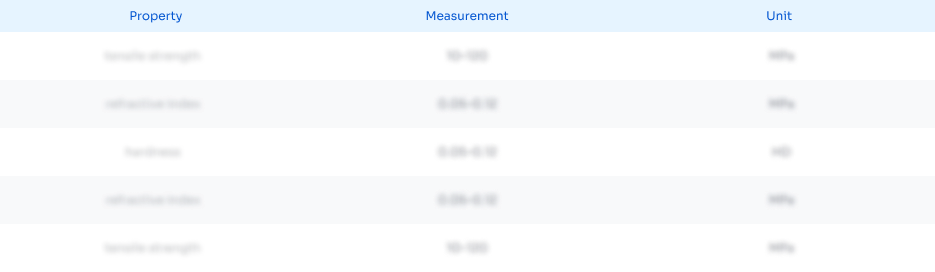
Abstract
Description
Claims
Application Information

- Generate Ideas
- Intellectual Property
- Life Sciences
- Materials
- Tech Scout
- Unparalleled Data Quality
- Higher Quality Content
- 60% Fewer Hallucinations
Browse by: Latest US Patents, China's latest patents, Technical Efficacy Thesaurus, Application Domain, Technology Topic, Popular Technical Reports.
© 2025 PatSnap. All rights reserved.Legal|Privacy policy|Modern Slavery Act Transparency Statement|Sitemap|About US| Contact US: help@patsnap.com