Fiber self-dense concrete composition, sound barrier and manufacture method thereof
A self-compacting concrete and composition technology, applied in the field of sound absorption and sound insulation products, can solve the problems of poor sound absorption and sound insulation effects, and achieve superior physical mechanics, beautiful decoration, and good sound absorption effects
- Summary
- Abstract
- Description
- Claims
- Application Information
AI Technical Summary
Problems solved by technology
Method used
Image
Examples
Embodiment 1
[0026] A fiber self-compacting concrete composition for sound-absorbing and insulating barriers, prepared from the following raw materials (kg): cement 1, sand 1.2, water 0.35, polycarboxylate superplasticizer 0.0061, glass fiber 0.01, polypropylene Fiber 0.001.
[0027] Preparation method: The order of raw material feeding is to put sand first and then cement, then turn on the mixer for dry mixing, add glass fiber and polypropylene fiber fiber during the dry mixing process, add water reducer and water after the materials are evenly dispersed, add water and water reducer Stir again to ensure that the mixture is uniform; then pour, solidify and demould; vibrate for 5-8 seconds during the pour to make the concrete surface dense and get rid of larger air bubbles in the concrete; to avoid mixing Control the water content of the sand to 1.4%-1.6% of the sand mass. In order to avoid the phenomenon of insufficient fluidity or bleeding of fiber self-compacting concrete, the amount of ...
Embodiment 2
[0029] A fiber self-compacting concrete composition for sound-absorbing barriers, prepared from the following raw materials (kg): cement 1, sand 1, water 0.3, polycarboxylate superplasticizer 0.0056, glass fiber 0.005, polypropylene Fiber 0.0005.
[0030] Preparation method: The order of raw material feeding is to put sand first and then cement, then turn on the mixer for dry mixing, add glass fiber and polypropylene fiber fiber during the dry mixing process, add water reducer and water after the materials are evenly dispersed, add water and water reducer Stir again to ensure that the mixture is uniform; then cast the mold, solidify and demould.
Embodiment 3
[0032] A fiber self-compacting concrete composition for sound-absorbing barriers, prepared from the following raw materials (kg): cement 1, sand 1.5, water 0.4, polycarboxylate superplasticizer 0.0066, glass fiber 0.015, polypropylene Fiber 0.0015.
[0033] Preparation method: with embodiment 1.
PUM
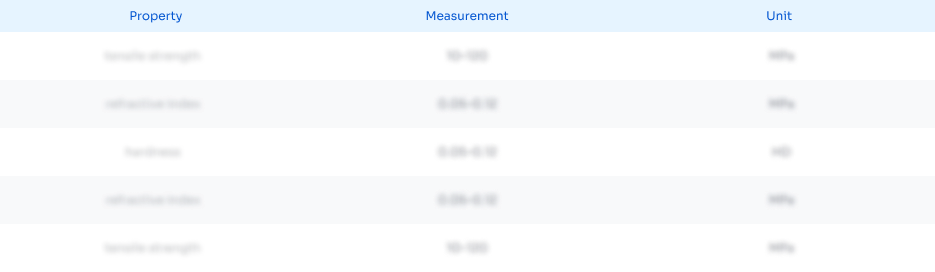
Abstract
Description
Claims
Application Information

- R&D
- Intellectual Property
- Life Sciences
- Materials
- Tech Scout
- Unparalleled Data Quality
- Higher Quality Content
- 60% Fewer Hallucinations
Browse by: Latest US Patents, China's latest patents, Technical Efficacy Thesaurus, Application Domain, Technology Topic, Popular Technical Reports.
© 2025 PatSnap. All rights reserved.Legal|Privacy policy|Modern Slavery Act Transparency Statement|Sitemap|About US| Contact US: help@patsnap.com