Method for prepring and modifying high heat-resistant aluminium hydroxide
A technology of aluminum hydroxide and high heat resistance, applied in the direction of alumina/aluminum hydroxide, etc., can solve the problems that the initial decomposition temperature is difficult to further increase, and the scope of application is difficult to further expand, so as to simplify the surface modification process and improve heat resistance properties, and the effect of improving heat resistance
- Summary
- Abstract
- Description
- Claims
- Application Information
AI Technical Summary
Problems solved by technology
Method used
Examples
Embodiment 1
[0022] First prepare the composite modifier: take the rare earth coupling agent REC (manufactured by the Guangzhou Institute of Chemistry, Chinese Academy of Sciences) and the phosphoric acid ester compound ethylphosphonic acid diethyl ester according to the weight ratio of 5:1, and then mix it physically. have to;
[0023] By weight percentage, get aluminum hydroxide 30%, ionized water 66.0%, composite modifier 4.0%,
[0024] Then put conventional aluminum hydroxide (700-1350 mesh) in a reactor with a stirring device, add deionized water, heat to a temperature of 60°C at a stirring speed of 1000 rpm (rpm), and then add a compound modification modified aluminum hydroxide, reacted for 20 minutes, filtered, dried at 100°C for 3 hours, and ground to obtain modified aluminum hydroxide. Its properties are shown in Table 1 below.
[0025] modifier
Embodiment 2
[0027] First prepare the composite modifier: take the rare earth coupling agent REC (manufactured by the Guangzhou Institute of Chemistry, Chinese Academy of Sciences) and the phosphoric acid ester compound ethylphosphonic acid diethyl ester according to the weight ratio of 5:1, and then mix it physically. have to;
[0028]Then by weight percentage, get aluminum hydroxide 25.5%, ionized water 73.0%, composite modifier 1.5%,
[0029] Then put conventional aluminum hydroxide (700-1350 mesh) in the container, add deionized water, heat to a temperature of 60°C at a stirring speed of 1000 rpm (rpm), and then add a composite modifier for modification. After reacting for 20 minutes, filter, dry at 110° C. for 3 hours, and grind to obtain modified aluminum hydroxide. Its performance after measurement is shown in Table 2 below.
[0030] modifier
Embodiment 3
[0032] Adopt dry process, get aluminum hydroxide 96%, rare earth coupling agent REC4% according to weight percentage,
[0033] Then put the aluminum hydroxide in a high-speed kneader, add rare earth coupling agent REC for high-speed (spindle speed 460-920 rpm) kneading modification, modification temperature 75 ° C, high-speed kneading for 10 minutes and then discharge. The performance of the aluminum hydroxide after the determination is shown in the following table 1.
[0034] modifier
Initial decomposition temperature (°C)
Activation index
Oil absorption value(g / g)
Rare earth coupling agent REC
260
78%
0.27
[0035] From the test results listed in the above tables 1, 2, and 3, it can be seen that the present invention has reached the requirements proposed by the object of the invention, and the modified aluminum hydroxide has good heat resistance and surface activity.
[0036] For the convenience of those skilled in the ar...
PUM
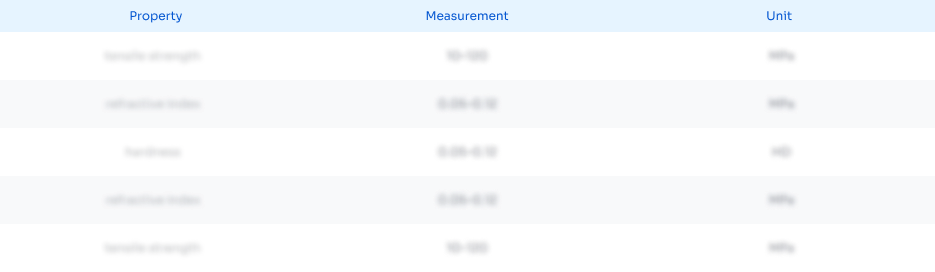
Abstract
Description
Claims
Application Information

- R&D Engineer
- R&D Manager
- IP Professional
- Industry Leading Data Capabilities
- Powerful AI technology
- Patent DNA Extraction
Browse by: Latest US Patents, China's latest patents, Technical Efficacy Thesaurus, Application Domain, Technology Topic, Popular Technical Reports.
© 2024 PatSnap. All rights reserved.Legal|Privacy policy|Modern Slavery Act Transparency Statement|Sitemap|About US| Contact US: help@patsnap.com