Helical bracket manufacturing method and helical bracket
A manufacturing method and helical technology, applied in the directions of overhead installation, supporting insulator, cable installation, etc., can solve the problems of center deviation and coating center deviation, and achieve the effect of prolonging life, high insulation strength and improving wire coating damage.
- Summary
- Abstract
- Description
- Claims
- Application Information
AI Technical Summary
Problems solved by technology
Method used
Image
Examples
Embodiment Construction
[0035] Embodiments of the present invention will be described below with reference to the drawings. figure 1 It is a schematic diagram of a device for feeding the tough metal core wire 2 wound on a spool forward (to the right in the figure).
[0036] In this figure, reference numerals 5, 5... denote feed rollers, which are respectively arranged in a pair up and down, and are driven by a driving device not shown, and feed the metal wire 2 between grooves provided around the rollers. Here, reference numeral 3 is a guide roll, and reference numeral 4 is a straightening roll.
[0037] And, when the feed rollers 5, 5, ... are rotated, the metal core wire 2 can be fed forward, that is, toward the direction of the guide pipe 7.
[0038] Next, the metal core wire 2 fed by the above-mentioned process is introduced into the mold 8 provided with the long helical two-stage hole, and while it is forced to pass through the mold 8 to form the long helical metal wire, the long helical wire i...
PUM
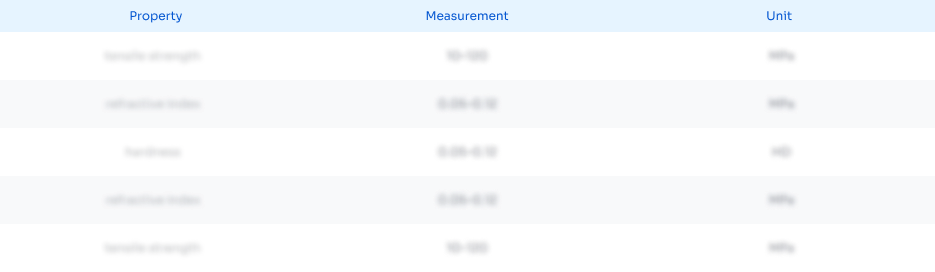
Abstract
Description
Claims
Application Information

- R&D
- Intellectual Property
- Life Sciences
- Materials
- Tech Scout
- Unparalleled Data Quality
- Higher Quality Content
- 60% Fewer Hallucinations
Browse by: Latest US Patents, China's latest patents, Technical Efficacy Thesaurus, Application Domain, Technology Topic, Popular Technical Reports.
© 2025 PatSnap. All rights reserved.Legal|Privacy policy|Modern Slavery Act Transparency Statement|Sitemap|About US| Contact US: help@patsnap.com