Multistage atomizing spray anti-rust oil process
A process method and technology of anti-rust oil, which is applied to door/window accessories, hinges without pins, hinge plates, etc., can solve problems such as uneven oil layer on the surface, uneven thickness of coating film, environmental pollution, etc., and achieve high efficiency and energy saving Production efficiency, easy automation, and improved utilization
- Summary
- Abstract
- Description
- Claims
- Application Information
AI Technical Summary
Problems solved by technology
Method used
Image
Examples
Embodiment Construction
[0012] The present invention is achieved in this way, and will be described in detail below in conjunction with the accompanying drawings. See figure 1 , is the multi-stage atomization spraying anti-rust oil process flow chart of the present invention.
[0013] The air atomizing device 1 feeds the compressed air generated by the air compressor 13 to suck out the antirust oil in the oil storage tank 16 and atomize it in the atomizing chamber 2 . The venturi diffusion throat 3 is diffused to the diffusion chamber 4, and the atomized anti-rust oil passing through the diffusion chamber 4 is evenly diffused, and the oil mist in the diffusion chamber is uniformly dispersed and the pressure and flow are slowed down. The oil mist is evenly and slowly sprayed out through the atomizing nozzle 5 at the outlet of the diffusion chamber. The outlet atomizing nozzle 5 and the charging electrode 8 of the diffusion chamber pass through the high-voltage electric field established by the high-...
PUM
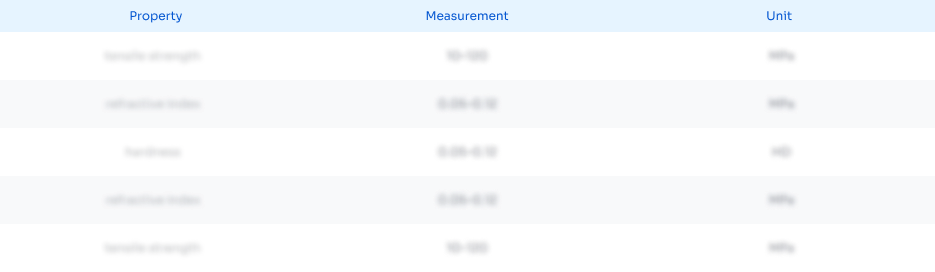
Abstract
Description
Claims
Application Information

- R&D
- Intellectual Property
- Life Sciences
- Materials
- Tech Scout
- Unparalleled Data Quality
- Higher Quality Content
- 60% Fewer Hallucinations
Browse by: Latest US Patents, China's latest patents, Technical Efficacy Thesaurus, Application Domain, Technology Topic, Popular Technical Reports.
© 2025 PatSnap. All rights reserved.Legal|Privacy policy|Modern Slavery Act Transparency Statement|Sitemap|About US| Contact US: help@patsnap.com