Refining slag for ultra-pure steel and preparation method thereof
A technology of ultra-pure steel and refining slag, applied in the direction of improving process efficiency, etc., can solve the problems of inability to reduce or remove harmful components, low purity of refining slag, increase of harmful components, etc., to improve the purity of molten steel and gas generation time Long-term, reduce the effect of harmful impurities
- Summary
- Abstract
- Description
- Claims
- Application Information
AI Technical Summary
Problems solved by technology
Method used
Examples
Embodiment 1
[0026] Embodiment 1: Take CaO≥53%, SiO 2 ≤1.5%, TiO 2 Limestone ≤50ppm, industrial alumina, the ratio of the two is 70:30, argon gas is introduced in the molten state, and TiO can be reduced from the raw materials. 2 Calcium powder reducing agent with the amount of iron oxide is made into a pre-melt and pulverized. The chemical composition of the resulting refining slag is CaO55wt%, Al 2 o 3 43wt%, SiO 2 1.9wt% of which TiO 2 ≤32ppm, N≤200ppm, (B+Pb)≤50ppm, (S+P)≤160ppm (the margin of the value is subtracted from ignition).
Embodiment 2
[0027] Embodiment 2: as embodiment 1, make pre-melt pulverization, grind to 200 mesh powder, add 5% C≥99%, N≤200ppm petroleum coke, 5% chemically pure barium carbonate, use high-speed mixer Mix evenly without adding any binder, at a pressure of 280kg / cm 2 Press down to form a flat spherical shape of 50×25×15mm. The chemical composition of the obtained refining slag is CaO49.5wt%, Al 2 o 3 38.7wt%, SiO 2 1.55wt%, BaCO 3 5wt%, C 5wt%, wherein TiO2≤32ppm, N≤200ppm, (B+Pb)≤50ppm, (S+P)≤160ppm.
PUM
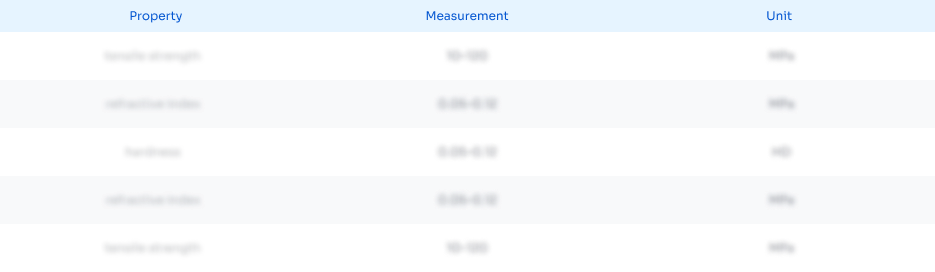
Abstract
Description
Claims
Application Information

- R&D
- Intellectual Property
- Life Sciences
- Materials
- Tech Scout
- Unparalleled Data Quality
- Higher Quality Content
- 60% Fewer Hallucinations
Browse by: Latest US Patents, China's latest patents, Technical Efficacy Thesaurus, Application Domain, Technology Topic, Popular Technical Reports.
© 2025 PatSnap. All rights reserved.Legal|Privacy policy|Modern Slavery Act Transparency Statement|Sitemap|About US| Contact US: help@patsnap.com