Hydraulic flexible method for producing cold-drawn pipe and apparatus
A cold-drawn and flexible technology, applied in wire drawing dies, mandrels, etc., can solve the problems of affecting product accuracy, lack of reliable control, lubricant leakage, etc., to achieve simple and convenient operation, eliminate vibration, and reduce manufacturing costs. Effect
- Summary
- Abstract
- Description
- Claims
- Application Information
AI Technical Summary
Problems solved by technology
Method used
Image
Examples
Embodiment Construction
[0055] The specific process steps of a kind of hydraulic flexible cold drawn pipe method are:
[0056] (1) Start to push the assembly oil cylinder 3, and pull the assembly 5 and the mold 8 to separate;
[0057] (2) The feeding frame 7 rises to make the tube blank 12 in place;
[0058] (3) Start the mandrel pushing oil cylinder 2, insert the mandrel 5-5 into the tube blank, push the tube blank into the mold 8, and the loading rack 7 descends;
[0059] (4) Push the combined body oil cylinder 3 to push the combined body 5 to the mold base, and at the same time, the piston 5-3 follows the movement, and the cylinder body 5-1 and the mold base 8-1 port are closed to complete the sealing;
[0060] (5) Start to push the piston oil cylinder 1, and push the piston 5-3 of the assembly 5 to support the tail of the tube blank;
[0061] (6) The clamping mechanism 10 acts to clamp the tube blank 12;
[0062] (7) start drawing oil cylinder 11, start drawing;
[0063] (8) The oil pressure ...
PUM
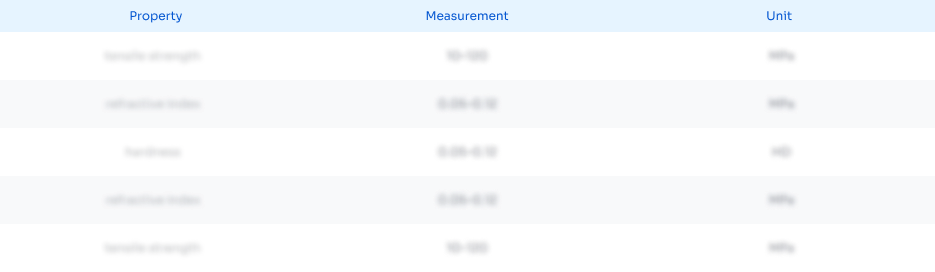
Abstract
Description
Claims
Application Information

- R&D Engineer
- R&D Manager
- IP Professional
- Industry Leading Data Capabilities
- Powerful AI technology
- Patent DNA Extraction
Browse by: Latest US Patents, China's latest patents, Technical Efficacy Thesaurus, Application Domain, Technology Topic, Popular Technical Reports.
© 2024 PatSnap. All rights reserved.Legal|Privacy policy|Modern Slavery Act Transparency Statement|Sitemap|About US| Contact US: help@patsnap.com