Machining method of workpiece welding groove-workpiece rotary type numerical control cutting machine
A welding groove and cutting processing technology, which is applied in cutting and industrial welding fields, can solve the problems of high manufacturing cost and complex structure, and achieve the effects of low manufacturing cost, fast workpiece positioning and safe use
- Summary
- Abstract
- Description
- Claims
- Application Information
AI Technical Summary
Problems solved by technology
Method used
Image
Examples
Embodiment Construction
[0012] exist figure 1 and figure 2 In the method embodiment shown, the base (1) is the basis for the realization of the entire method, and the workpiece infinite rotary table (3) and the infinite rotary table power transmission (2) are installed in the middle, and the workpiece infinite rotary table (3) carries the workpiece to be cut. For the workpiece, a cutting torch longitudinal movement mechanism (8) is installed on the left side of the base (1), the longitudinal slide plate (11) on the mechanism is driven by the cutting torch longitudinal drive device (15) to realize longitudinal movement, and the longitudinal slide plate (11 ) is connected with the crossbeam (12), and the cutting torch horizontal linear motion mechanism (7) is installed on the crossbeam (12). A cutting torch elevating device (6) is housed on the transverse slide plate (14), a cutting torch swinging device (4) is housed on the cutting torch lifting device (6), and a cutting torch (4) for cutting is ins...
PUM
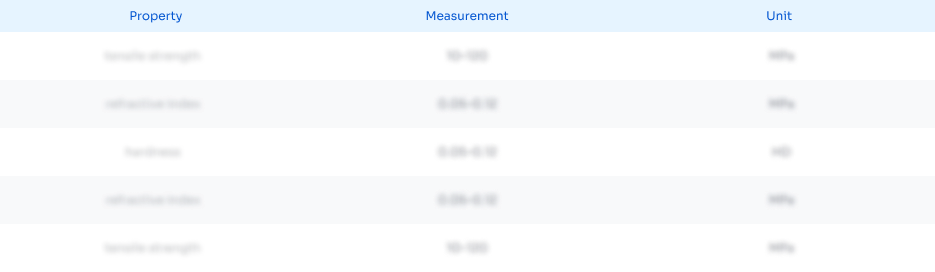
Abstract
Description
Claims
Application Information

- R&D Engineer
- R&D Manager
- IP Professional
- Industry Leading Data Capabilities
- Powerful AI technology
- Patent DNA Extraction
Browse by: Latest US Patents, China's latest patents, Technical Efficacy Thesaurus, Application Domain, Technology Topic, Popular Technical Reports.
© 2024 PatSnap. All rights reserved.Legal|Privacy policy|Modern Slavery Act Transparency Statement|Sitemap|About US| Contact US: help@patsnap.com