Mold release composition and process therewith
A technology of composition and solvent, which is applied in the field of release agent composition and its application, can solve the problems of not being able to obtain a continuous film, not being able to coat the surface well, etc.
- Summary
- Abstract
- Description
- Claims
- Application Information
AI Technical Summary
Problems solved by technology
Method used
Examples
Embodiment 1
[0024] EXAMPLE 1 This example demonstrates that thinner continuous silicone resin coatings can be obtained with volatile methyl silicones than with petroleum ether.
[0025] The release agent composition comprising the following components is sprayed in the amount shown in the table below on a 1 inch × 3 inch (2.54cm × 7.62cm) microscope slide that has been weighed and heated to 65°C in advance: 80% solvent ( Petroleum ether or octamethylcyclotetrasiloxane (volatile methyl)), 20% silicone resin and fluid, and about 0.2% catalyst (based on the total weight of solvent, resin and fluid; TYZOR TBT and dibutyltin diacetate). After allowing sufficient time for the solvent to evaporate in the fume hood, the release agent was cured at 65°C for 2 minutes. Slides were then reweighed and visually inspected under a microscope to estimate the silicone resin coverage of the slide surface. The results are shown in Table 1.
[0026] Coating weight (mg)
[0027] On glass slides ...
Embodiment 2
[0028] EXAMPLE 2 This example illustrates how various methyl silicone solvents can be used to promote smooth, continuous coatings of various silicone resins, fluids and functional fluids applied at elevated temperatures.
[0029] Silicone resins, fluids and functional fluids were dispersed in various hydrocarbon solvents and volatile methyl siloxanes at concentrations of 5% by weight polymer solids and 95% by weight solvent. Silicone polymers and solvents were sprayed with a Preval sprayer onto pre-weighed 1 inch by 3 inch (2.54 cm by 7.62 cm) microscope slides heated to 65°C. After the solvent evaporated, the glass slide was weighed to determine the coating weight and the smoothness and coverage of the coating were visually inspected, as shown in Table 2.
[0030] coating
coating
SP 1
solvent 2
weight
(mg)
appearance
coverage
SP 1
solvent 2
weight
...
Embodiment 3
[0034] EXAMPLE 3 This example illustrates how a volatile methylsiloxane solvent can be used to promote smooth, continuous coatings of room temperature coated silicone polymers.
[0035] One sample of silicone rubber was dispersed in petroleum ether, while a second sample of the same silicone rubber was dispersed in OMS fluid at a concentration of 5% by weight polymer solids and 95% by weight solvent. The silicone polymer and solvent were sprayed onto pre-weighed 1 inch by 3 inch (2.54 cm by 7.62 cm) room temperature microscope slides with a Preval sprayer. After the solvent evaporated, the glass slide was weighed to determine the coating weight and the smoothness and coverage of the coating were visually inspected. The results are shown in Table 3.
[0036] coating
coating
SP 1
solvent 2
weight
(mg)
appearance
coverage
SP 1
solvent 2
weight
(mg)
...
PUM
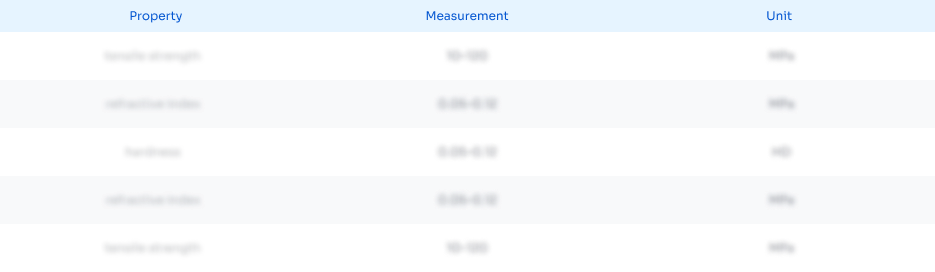
Abstract
Description
Claims
Application Information

- R&D
- Intellectual Property
- Life Sciences
- Materials
- Tech Scout
- Unparalleled Data Quality
- Higher Quality Content
- 60% Fewer Hallucinations
Browse by: Latest US Patents, China's latest patents, Technical Efficacy Thesaurus, Application Domain, Technology Topic, Popular Technical Reports.
© 2025 PatSnap. All rights reserved.Legal|Privacy policy|Modern Slavery Act Transparency Statement|Sitemap|About US| Contact US: help@patsnap.com