Speed controller of synchronous motor
A control device and pulse width control technology, applied in the direction of motor generator control, AC motor control, single motor speed/torque control, etc., can solve the problem of difficult to reproduce current, difficult to achieve high-speed and high-performance Harmonic increase and other issues
- Summary
- Abstract
- Description
- Claims
- Application Information
AI Technical Summary
Problems solved by technology
Method used
Image
Examples
Embodiment Construction
[0062] Hereinafter, an embodiment of the present invention will be described with reference to the drawings.
[0063] Embodiment 1
[0064] Fig. 1 is a block diagram showing a system configuration of Embodiment 1 of a speed control device for a synchronous motor according to the present invention. In Fig. 1, the speed control device of the synchronous motor is constituted as having a generator for providing the rotational speed command ωr to the synchronous motor 5 * The revolution command ωr * The number of revolutions instruction generator 1 of computing; The AC applied voltage of synchronous motor 5 is calculated, according to this calculation result, generates the pulse width modulation signal (PWM signal) as pulse width control signal, is applied to the controller 2 on the inverter 3; Inverter 3 driven by this PWM signal; DC power supply 4 to supply power to inverter 3; current detector (inverter current The detector) 6 is connected to the AC output side of the inverte...
PUM
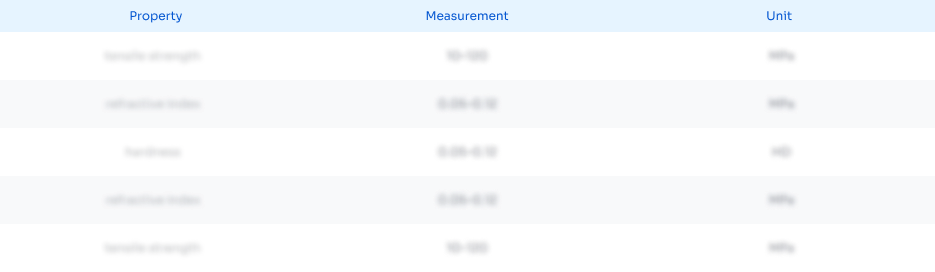
Abstract
Description
Claims
Application Information

- R&D Engineer
- R&D Manager
- IP Professional
- Industry Leading Data Capabilities
- Powerful AI technology
- Patent DNA Extraction
Browse by: Latest US Patents, China's latest patents, Technical Efficacy Thesaurus, Application Domain, Technology Topic, Popular Technical Reports.
© 2024 PatSnap. All rights reserved.Legal|Privacy policy|Modern Slavery Act Transparency Statement|Sitemap|About US| Contact US: help@patsnap.com