Method of preparing two kinds of perferrate at the same time
A ferrate and potassium ferrate technology, applied in chemical instruments and methods, iron compounds, sodium/potassium compounds, etc., can solve the problems of many by-products, explosion, and high power consumption
- Summary
- Abstract
- Description
- Claims
- Application Information
AI Technical Summary
Problems solved by technology
Method used
Examples
Embodiment 1
[0026] Example 1: prepare 1L of KOH solution of 10mol / L, add 1g of potassium iodide as a stabilizer in the solution, feed chlorine gas into the KOH solution for 2h, and keep the temperature of the KOH solution at 30°C; then add 600g of KOH solid and stir to dissolve, control During this operation, the temperature of the solution does not exceed 35°C; the solution is cooled to 10°C and filtered, and the filtrate containing potassium hypochlorite is collected. The concentration of potassium hypochlorite in the filtrate is about 0.5mol / L, and the filter residue is mainly KCl, which is used as a by-product; Add the collected potassium hypochlorite solution and react at 25°C for 1h; stir 1L of 10mol / L KOH solution that has been cooled to 0°C for 10min and then filter, the filter residue is the crude product of potassium ferrate, and the filtrate mainly contains KOH, which is recycled ;Dissolve the crude product in 300mL 3mol / L KOH solution, and quickly filter it into an equal volume...
Embodiment 2
[0027] Example 2: Prepare 1L of KOH solution of 15mol / L, add 2g of potassium iodide as a stabilizer in the solution, feed chlorine gas into the KOH solution for 10h, and keep the temperature of the KOH solution at 0°C: then add 1000g of KOH solid and stir to dissolve, When controlling this operation, the temperature of the solution does not exceed 35°C; the solution is cooled to -10°C and filtered, and the filtrate containing potassium hypochlorite is collected. The concentration of potassium hypochlorite in the filtrate is about 1.5mol / L, and the filter residue is mainly KCl, which is used as a by-product; 150g Add ferric nitrate to the collected potassium hypochlorite solution and react at 25°C for 5 hours; stir 1L of 10mol / L KOH solution that has been cooled to 0°C for 5-10min and then filter. The filter residue is the crude product of potassium ferrate, and the filtrate mainly contains KOH, recycling; dissolve the crude product in 1.2L 3mol / L KOH solution, and quickly filte...
Embodiment 3
[0028] Embodiment 3: Similar to Examples 1 and 2, the difference is that 1.5g of potassium iodide is added as a stabilizing agent in the KOH solution, chlorine gas is passed into the KOH solution for 5h, and the temperature of the KOH solution is kept at 15°C; then 800g of KOH solid is added and Stir to dissolve, and control the temperature of the solution during this operation to not exceed 35°C; cool the solution to 2°C and filter, collect the filtrate containing potassium hypochlorite, the concentration of potassium hypochlorite in the filtrate is about 1.0mol / L, and the filter residue is mainly KCl, as a by-product; Add 100g of ferric sulfate to the collected potassium hypochlorite solution and react at 35°C for 2h; stir 1L of 10mol / L KOH solution that has been cooled to 0°C for 5min and then filter, the filter residue is the crude product of potassium ferrate, and the filtrate mainly contains KOH, recycling; dissolve the crude product in 150mL of 1.5mol / L KOH solution, and...
PUM
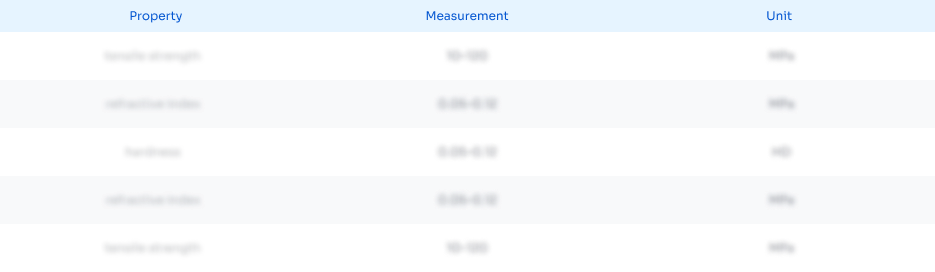
Abstract
Description
Claims
Application Information

- R&D
- Intellectual Property
- Life Sciences
- Materials
- Tech Scout
- Unparalleled Data Quality
- Higher Quality Content
- 60% Fewer Hallucinations
Browse by: Latest US Patents, China's latest patents, Technical Efficacy Thesaurus, Application Domain, Technology Topic, Popular Technical Reports.
© 2025 PatSnap. All rights reserved.Legal|Privacy policy|Modern Slavery Act Transparency Statement|Sitemap|About US| Contact US: help@patsnap.com