Making process of large titanium cathode roller cylinder and composite great current cathode roller
A manufacturing method and cathode roller technology, applied in the direction of the electrode, etc., can solve the problems affecting the normal use of the foil material quality of the cathode roller, affecting the uniformity of the surface current of the titanium cylinder, and affecting the uniformity of conductivity, etc., achieving low cost and improving the uniformity of conductivity , to ensure the effect of stiffness
- Summary
- Abstract
- Description
- Claims
- Application Information
AI Technical Summary
Problems solved by technology
Method used
Image
Examples
Embodiment Construction
[0025] combined with figure 1 , 2 , 3 describe an embodiment of the present invention.
[0026] Manufacturing method of large-scale titanium cathode roller body:
[0027] 1. Heating both ends of the titanium plate to 400-500°C and then molding it to form a flange with a height greater than 70% of the forging deformation to the outside;
[0028] 2. Roll the titanium plate into a cylinder so that the molded flanges are butted, and the joints are fully welded. The welding current is controlled between 100 and 200A, and X-ray inspection is carried out to make the weld reach JB4730 Grade I or above in the -94 standard.
[0029] 3. Forging the weld seam four times after high-frequency induction heating, the first forging deformation is controlled at about 25%, the temperature is controlled at about 1000°C, the second forging deformation is controlled at about 30%, and the temperature is controlled at 950 ℃, the deformation amount of the third forging is controlled at about 30%, ...
PUM
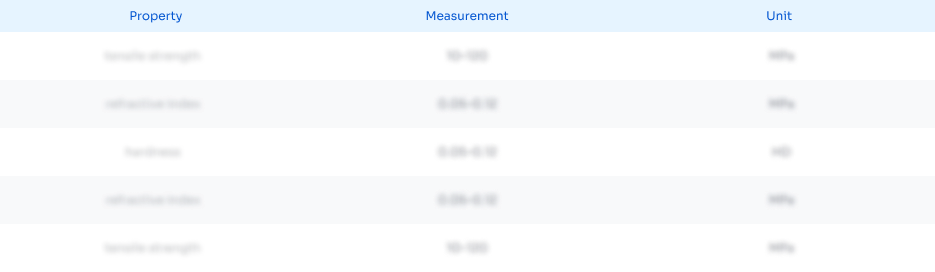
Abstract
Description
Claims
Application Information

- R&D
- Intellectual Property
- Life Sciences
- Materials
- Tech Scout
- Unparalleled Data Quality
- Higher Quality Content
- 60% Fewer Hallucinations
Browse by: Latest US Patents, China's latest patents, Technical Efficacy Thesaurus, Application Domain, Technology Topic, Popular Technical Reports.
© 2025 PatSnap. All rights reserved.Legal|Privacy policy|Modern Slavery Act Transparency Statement|Sitemap|About US| Contact US: help@patsnap.com