Refractory composite heat insulating sprayed material
A composite thermal insulation and high temperature resistant technology, which is applied in the direction of fireproof coatings, alkali metal silicate coatings, etc., can solve the problem of unsatisfactory technical performance and application effect of thermal insulation coatings, large batches, long-distance shipments, and inconvenient storage by manufacturers. Problems such as temperature cohesive force not meeting application requirements, etc., to achieve good thermal insulation performance, easy flaw detection and maintenance, and good sealing effect
- Summary
- Abstract
- Description
- Claims
- Application Information
AI Technical Summary
Problems solved by technology
Method used
Examples
Embodiment 1
[0010] The thermal insulation spray powder is composed of 25% by weight of sepiolite, 9% of brucite, 18% of crocidolite, 12% of basalt, 20% of andalusite, 15% of quartz stone, and 1% of bonding powder. formulated.
Embodiment 2
[0012] The thermal insulation spray powder is prepared by weight percentage: 30% of sepiolite, 10% of brucite, 20% of crocidolite, 13% of basalt, 10% of andalusite, 15% of quartz stone, and 2% of bonding powder made.
Embodiment 3
[0014] The thermal insulation spray powder is prepared by weight percentage: 20% sepiolite, 8.5% brucite, 15% crocidolite, 15% basalt, 20% andalusite, 20% quartz stone, and 1.5% bonding powder made.
[0015] In the thermal insulation spray paint of the present invention, since the spray powder contains functions of anticorrosion, oil resistance, acid resistance and alkali resistance, and strong adsorption and cohesive force, it is not necessary to carry out anticorrosion treatment on the equipment before construction, but to The powdery thermal insulation spraying powder is transported to the construction site, and after adding water and mixing it into a slurry, it can be directly sprayed or smeared on the equipment, which is both thermal insulation and anti-corrosion. In specific use, when it is necessary to prepare spray coatings, the weight ratio of thermal insulation spray powder to water is 1:2.5, and the spray slurry can be obtained after mixing evenly according to the p...
PUM
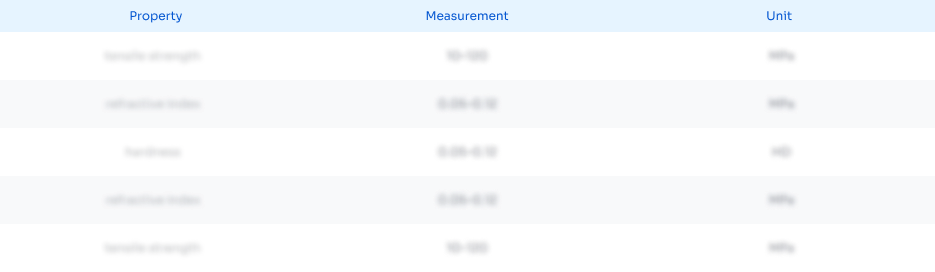
Abstract
Description
Claims
Application Information

- R&D
- Intellectual Property
- Life Sciences
- Materials
- Tech Scout
- Unparalleled Data Quality
- Higher Quality Content
- 60% Fewer Hallucinations
Browse by: Latest US Patents, China's latest patents, Technical Efficacy Thesaurus, Application Domain, Technology Topic, Popular Technical Reports.
© 2025 PatSnap. All rights reserved.Legal|Privacy policy|Modern Slavery Act Transparency Statement|Sitemap|About US| Contact US: help@patsnap.com