Electroplating additive and its preparation method
An electroplating additive and total weight technology, which is applied in the direction of metal processing equipment, manufacturing tools, welding equipment, etc., can solve the problems of easy turbidity, poor dispersion, and coarse crystallization of the plating solution, and achieve good weldability, eliminate compressive stress, and crystallization detailed effect
- Summary
- Abstract
- Description
- Claims
- Application Information
AI Technical Summary
Problems solved by technology
Method used
Examples
example 1
[0015] Example 1 (suitable for rack plating)
[0016] (1) formula (weight %):
[0017] Dodecylphenol ethoxylate 5
[0018] Polyoxyethylene aniline ether 1
[0019] N,N-diethyl-m-toluidine 1.2
[0020] Hydroxylactide 2.5
[0021] Acetylglycine 1.5
[0022] Naphthalenesulfonic acid 1
[0023] Propylene Glycol Polyoxyethylene Polyoxypropylene Ether 3
[0024] Hydroquinone 1
[0025] water 83.8
[0026] (2) Preparation method:
[0027] Weigh the required amount of deionized water into the reaction kettle, and heat to 45-55°C. In another reactor, mix N,N-diethyl-m-toluidine and hydroxypropionic acid, raise the temperature to 50° C., and stir for 10 minutes. The mixture of N,N-diethyl-m-toluidine and hydroxypropionic acid was added to deionized water with stirring. Then, add dodecylphenol polyoxyethylene ether, polyoxyethylene aniline ether, acetylglycine, naphthalenesulfonic acid, propylene glycol polyoxyethylene polyoxypropylene ether and hydroquinone in sequence. Cont...
example 2
[0028] Example 2 (suitable for high-speed plating)
[0029] (1) formula (weight %):
[0030] Dodecylphenol ethoxylate 3
[0031] Polyoxyethylene aniline ether 1
[0032] Dimethylaminopropylmethacrylamide 2
[0033] Acetylglycine 1.5
[0034] Naphthalenesulfonic acid 1
[0035] Internal glycol polyoxyethylene polyoxypropylene ether 3
[0036] Polyoxyethylene polyoxypropylene monobutyl ether 1
[0037] Hydroquinone 1
[0038] water 86.5
[0039] (2) Preparation method:
[0040] Weigh the required amount of deionized water into the reaction kettle, and heat to 45-55°C. Under stirring, add dodecylphenol polyoxyethylene ether, polyoxyethylene aniline ether, dimethylaminopropyl methacrylamide, acetylglycine, naphthalenesulfonic acid, propylene glycol polyoxyethylene polyoxypropylene ether, polyoxyethylene Ethylene polyoxypropylene monobutyl ether and hydroquinone. Continue to stir for 1 hour, filter, measure and pack into barrels.
PUM
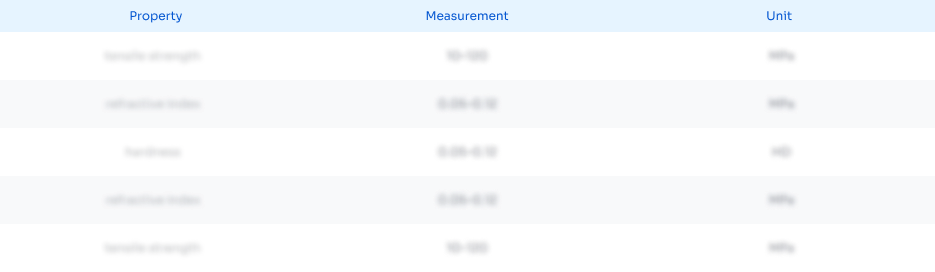
Abstract
Description
Claims
Application Information

- Generate Ideas
- Intellectual Property
- Life Sciences
- Materials
- Tech Scout
- Unparalleled Data Quality
- Higher Quality Content
- 60% Fewer Hallucinations
Browse by: Latest US Patents, China's latest patents, Technical Efficacy Thesaurus, Application Domain, Technology Topic, Popular Technical Reports.
© 2025 PatSnap. All rights reserved.Legal|Privacy policy|Modern Slavery Act Transparency Statement|Sitemap|About US| Contact US: help@patsnap.com